I have some questions on how people typically specify drag/collector loads to truss suppliers.
See diagram below as a simple example. I understand what the loads are doing in the diaphragm and in the shear wall. But I'm a little confused on what they do through the pre-engineered trusses.
1. For this example, would you specify loads on your plans in a "kip" or "klf" format? What value would you give (i.e. design all three drag trusses for 10 kips, design all for 4.2 kips, design end trusses for 3.3 kips and middle truss for 4.2 kips, or design all trusses for 0.167 klf unit shear)?
2. How exactly does the truss designer apply this force to their truss design? Added axial force to the top chord that they apply at the end of the truss? Unit shear that gets applied all along the top chord?
3. How does the truss designer resolve the force? For the middle truss, it would leave the truss through the bottom chord. If I locate the strap connecting the end and middle trusses at the top chord, the force would have to transfer out through that top chord of the end trusses. Is this something that goes into their truss design? Would it make a difference in their design?
See diagram below as a simple example. I understand what the loads are doing in the diaphragm and in the shear wall. But I'm a little confused on what they do through the pre-engineered trusses.
1. For this example, would you specify loads on your plans in a "kip" or "klf" format? What value would you give (i.e. design all three drag trusses for 10 kips, design all for 4.2 kips, design end trusses for 3.3 kips and middle truss for 4.2 kips, or design all trusses for 0.167 klf unit shear)?
2. How exactly does the truss designer apply this force to their truss design? Added axial force to the top chord that they apply at the end of the truss? Unit shear that gets applied all along the top chord?
3. How does the truss designer resolve the force? For the middle truss, it would leave the truss through the bottom chord. If I locate the strap connecting the end and middle trusses at the top chord, the force would have to transfer out through that top chord of the end trusses. Is this something that goes into their truss design? Would it make a difference in their design?
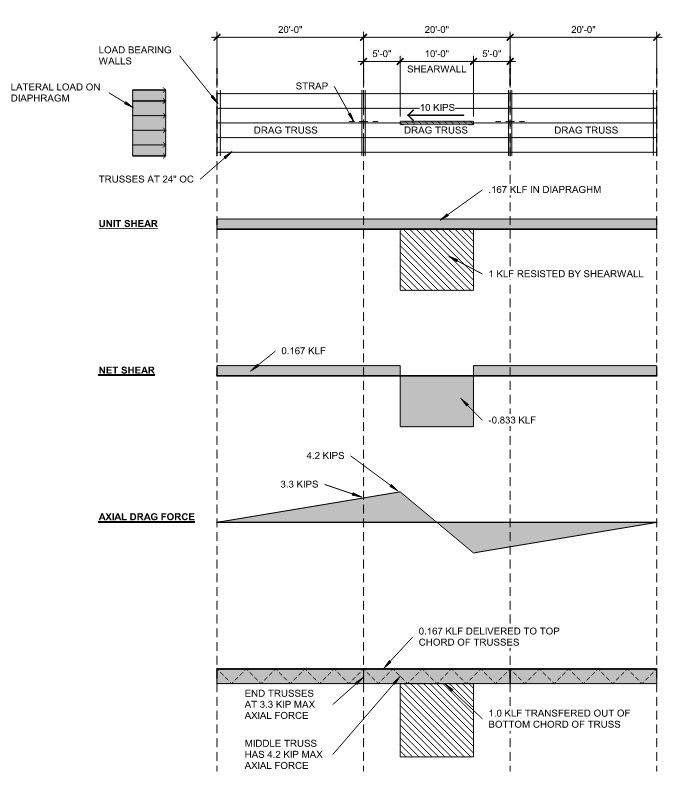