RFreund
Structural
- Aug 14, 2010
- 1,882
What is the "best" way to identify and calculate an HSS to HSS weld where the HSS dimensions match?
Will this follow a PJP T-Tubular connection? If so I'm a little confused on how to calculate this. Also the figure in table 8-2 page 8-64 in my 2010 edition gives a "C" dimension and also show a 1.5t.b or as required to flush out dimension and I'm not sure what this is for. Is this something that I designate or is that just part of the prequalified weld?
EIT
Will this follow a PJP T-Tubular connection? If so I'm a little confused on how to calculate this. Also the figure in table 8-2 page 8-64 in my 2010 edition gives a "C" dimension and also show a 1.5t.b or as required to flush out dimension and I'm not sure what this is for. Is this something that I designate or is that just part of the prequalified weld?
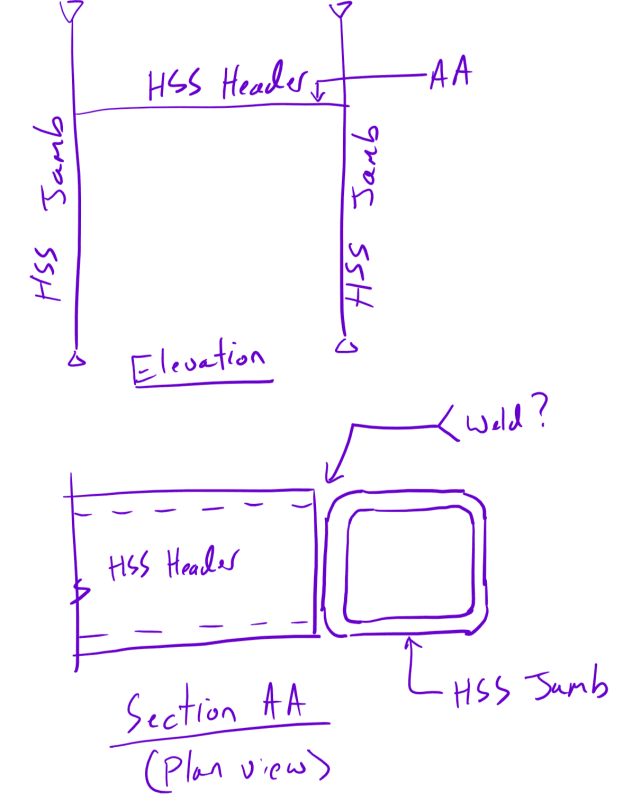
EIT