McMichael05
Structural
Need some help in determining if this connection adequate for the given loading. Its a HSS6x6x1/4 beam welded to another HSS6x6x1/4 beam. Calls for a 3/16 fillet weld around the whole member. Has a constant shear of 4.5k and a torsion of 0.365k-ft. Having a hard time determining the required depth of the weld needed. Any help would be appreciated. Thanks
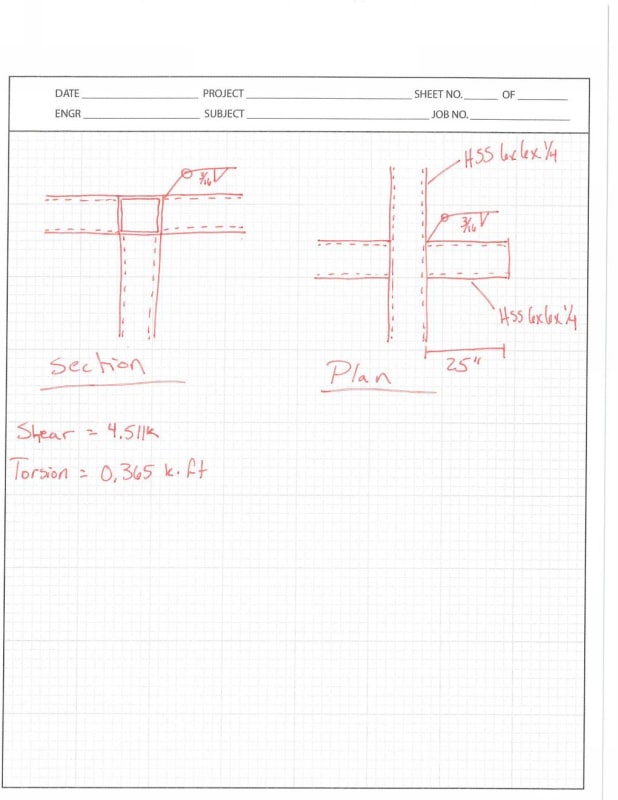