I am currently doing one project on hydraulic actuator synchronization using mechanical coupling( rigid coupling) as part of my internship. it is cost effective, don't have any complicated controls. just pump the fluid. since it is rigid and the mass is centralized the volume and pressure should be equal to both actuators.
This is the basic structure -->
when I was doing my research, I came across so many models which using other techniques like servo valves, but I hardly saw anything about the mechanical coupling., What are the disadvantages of this system?
PS- the connection is rigid, the weight is centralized, might have slight leakage (assuming, since it is for practical use).
This is the basic structure -->
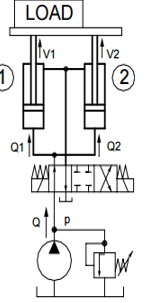
when I was doing my research, I came across so many models which using other techniques like servo valves, but I hardly saw anything about the mechanical coupling., What are the disadvantages of this system?
PS- the connection is rigid, the weight is centralized, might have slight leakage (assuming, since it is for practical use).