Hi
If I have a very simple steel frame with 2 steel columns and one 1 I-beam (UB) and BMD as shown below, how do I decide my beam critical length for LTB resistance at support under hogging moment? My software is using full span length but I was wondering whether it should be shorter as my bottom flange at mid-span will be under tension. Should it be the length from maximum moment to zero moment (point of contraflexure)?
Thanks
If I have a very simple steel frame with 2 steel columns and one 1 I-beam (UB) and BMD as shown below, how do I decide my beam critical length for LTB resistance at support under hogging moment? My software is using full span length but I was wondering whether it should be shorter as my bottom flange at mid-span will be under tension. Should it be the length from maximum moment to zero moment (point of contraflexure)?
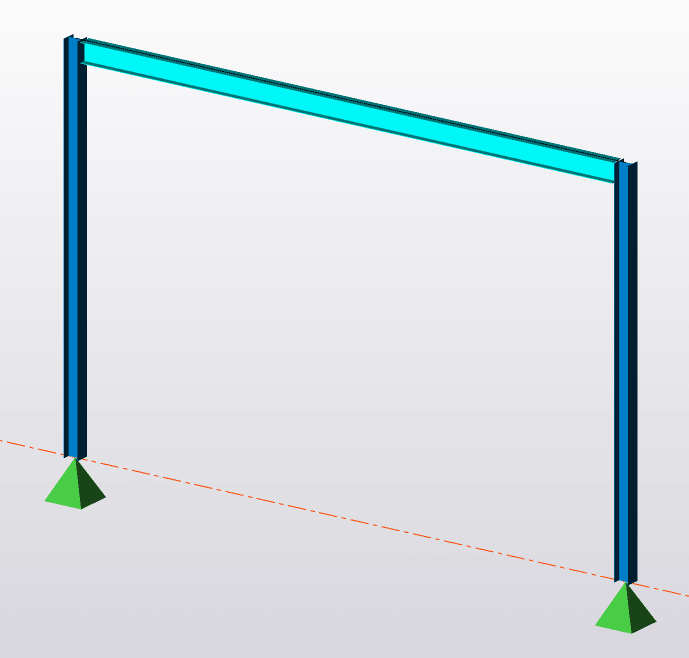
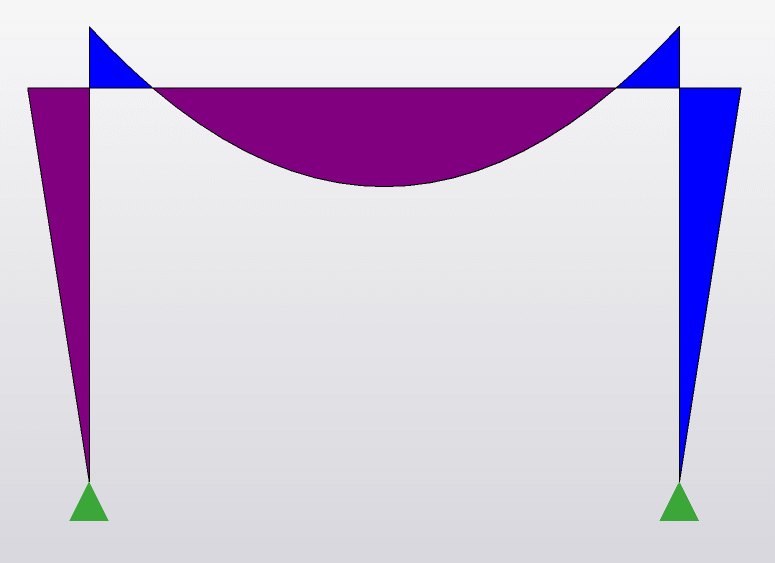
Thanks