This is the situation:
For clarity, this is a P&ID sketch of part of the same manifold:
I don't understand the position of the three way mixer, as this would mix hot water into the return and serves no function to control the heat of the flow to the HX - it could limit flow to the HX but this does not make much sense energetically (especially considering the cogeneration plant) There's another three way mixer installed near the boiler that could ensure a minimum return temp.
I also miss one-way valves at the pumps.
Context:
This is part of the heating system of a wastewater treatment plant
The large pipes/the right circuit in the P&ID supply the sewage sludge heat exchangers, the small pipe supplies building heating
The heat sources are a sewage gas fired cogeneration plant and a an oil fired boiler, AFAIK the cogenreation plant was added long after the boiler.
Both heat sources have their own feed pump and are connected in paralell, there's a hydraulic compensator
The plant operators could not explain their heating system to me (Lots of automation, sparse documentation)
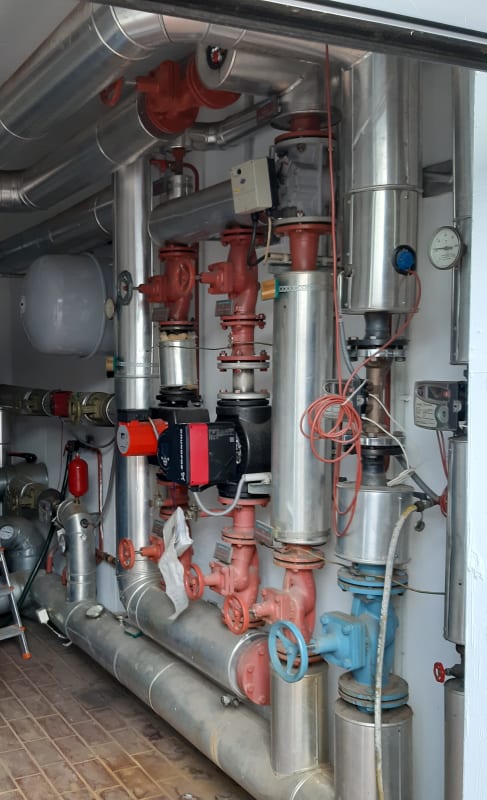
For clarity, this is a P&ID sketch of part of the same manifold:
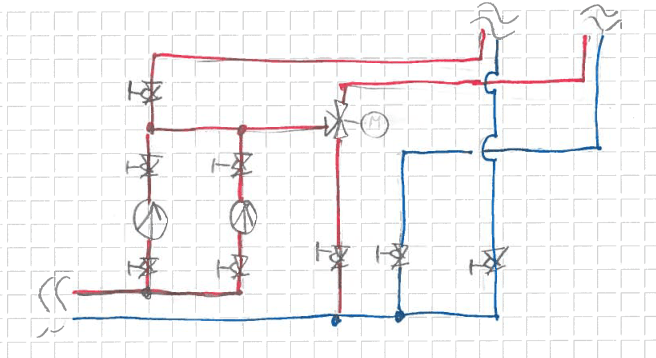
I don't understand the position of the three way mixer, as this would mix hot water into the return and serves no function to control the heat of the flow to the HX - it could limit flow to the HX but this does not make much sense energetically (especially considering the cogeneration plant) There's another three way mixer installed near the boiler that could ensure a minimum return temp.
I also miss one-way valves at the pumps.
Context:
This is part of the heating system of a wastewater treatment plant
The large pipes/the right circuit in the P&ID supply the sewage sludge heat exchangers, the small pipe supplies building heating
The heat sources are a sewage gas fired cogeneration plant and a an oil fired boiler, AFAIK the cogenreation plant was added long after the boiler.
Both heat sources have their own feed pump and are connected in paralell, there's a hydraulic compensator
The plant operators could not explain their heating system to me (Lots of automation, sparse documentation)