gotothesky
Mechanical
I would like to design Studding flanges for high pressure exchanger.
Commercial software for pressure vessel calculation dose not provide Design option of Studding flange.
Due to above reason, I have to make strength calculation sheet for flanges.
But, I am very sorry that I have a big problem during making calculation sheet.
In ASME Sec.VIII APP.2 Table 2-7.1, flange factors' Formulas are extremely complex!!
I checked Formulas so many times. But, I can't find out any error.
But results of F / V / f are minus values.
Is there any guy who can teach me what is wrong?
I attached excel sheet that I am making for flange calculation.
Regards,
Commercial software for pressure vessel calculation dose not provide Design option of Studding flange.
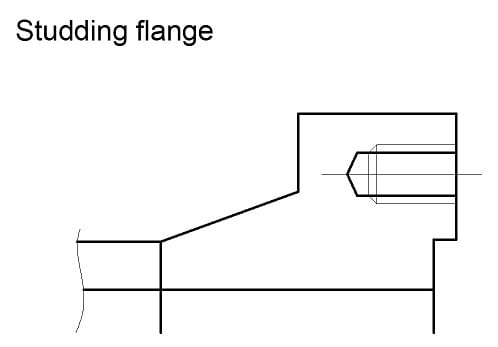
Due to above reason, I have to make strength calculation sheet for flanges.
But, I am very sorry that I have a big problem during making calculation sheet.
In ASME Sec.VIII APP.2 Table 2-7.1, flange factors' Formulas are extremely complex!!
I checked Formulas so many times. But, I can't find out any error.
But results of F / V / f are minus values.
Is there any guy who can teach me what is wrong?
I attached excel sheet that I am making for flange calculation.
Regards,