There are two identical 480V switchgears located 1000' apart. Both are fed through 12.47kV-480V, 1500kVA transformers. Both switchgears have a secondary main breaker and secondary feeder breakers. All the protection on the breakers are set up the same of the same size.
Here is the issue: Should a fault occur where shown on BUSWAY 1A the East Breaker will open - but because of all the resistance of the busway back to the West - it doesn't open it's paralleled breaker at the same time.
FDR BKR 2 WEST however does open, and so does the main on that side, cause they are faster.
What is desired to happen is that on a fault on the particular bus is that both breakers feeding it open - and none of the others.
Here is the issue: Should a fault occur where shown on BUSWAY 1A the East Breaker will open - but because of all the resistance of the busway back to the West - it doesn't open it's paralleled breaker at the same time.
FDR BKR 2 WEST however does open, and so does the main on that side, cause they are faster.
What is desired to happen is that on a fault on the particular bus is that both breakers feeding it open - and none of the others.
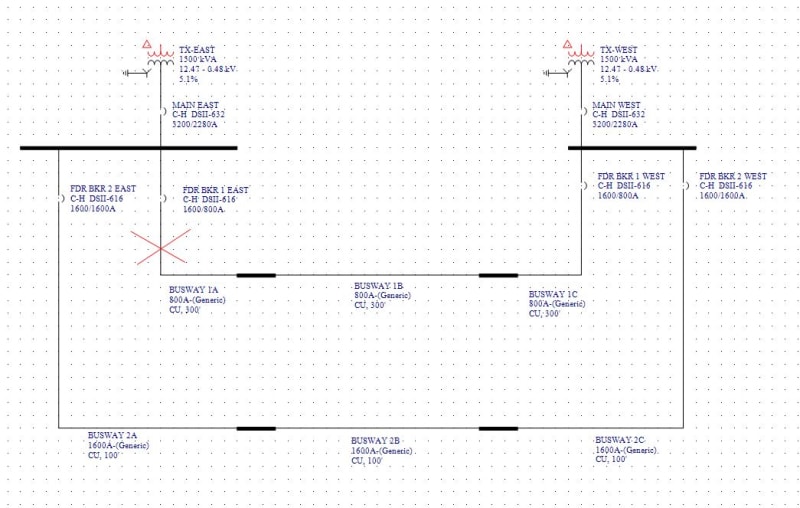