Hi guys,
I am currently working on a project with stiffened aluminium plates subjected to impact loading in order to replicate ship collisions. A part of the project is to validate my numerical model with experimental data from previous tests.
The model is pretty "basic": A 3d-deformable rig made of steel, with an aluminium plate that is simply supported on top of it. I run tests with both blunt and hemispherical indenters to find out how this affects the structural response. The impacts covered are in the low velocity regime, i.e. velocities between 0.4 - 0.6 m/s and inertia forces should not be a problem. Time period = 0.1 s
The plate is modelled using S4R elements, while the rig is modelled with C3D8R elements. The nose is discrete rigid.
The General Contact-algorithm is used in the simulations, with some excluded pairs (surface-to-surface between rig/plate and indenter/plate).
The problem I am having (as you can see from the plot below), is that the model is to stiff. I also have a "bump" in curve in the first steps of the analysis. I have made sure that the initial gap between the nose and the plate is sufficient (greater than the shell thicknes) and I have also implemented the smooth step-amplitude. Material properties used in the model are identical to the ones used in the laboratory.
The mesh size and the friction coefficients does not really have that big of an impact on the results.
Do you guys have any tips or input on what can be wrong with my model?
Thanks,
Even (Norway)
I am currently working on a project with stiffened aluminium plates subjected to impact loading in order to replicate ship collisions. A part of the project is to validate my numerical model with experimental data from previous tests.
The model is pretty "basic": A 3d-deformable rig made of steel, with an aluminium plate that is simply supported on top of it. I run tests with both blunt and hemispherical indenters to find out how this affects the structural response. The impacts covered are in the low velocity regime, i.e. velocities between 0.4 - 0.6 m/s and inertia forces should not be a problem. Time period = 0.1 s
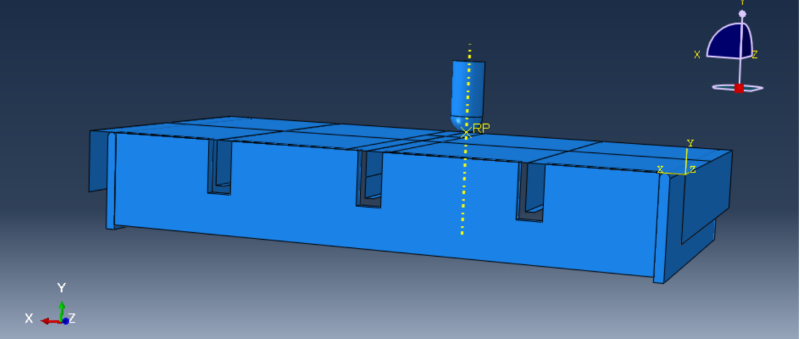
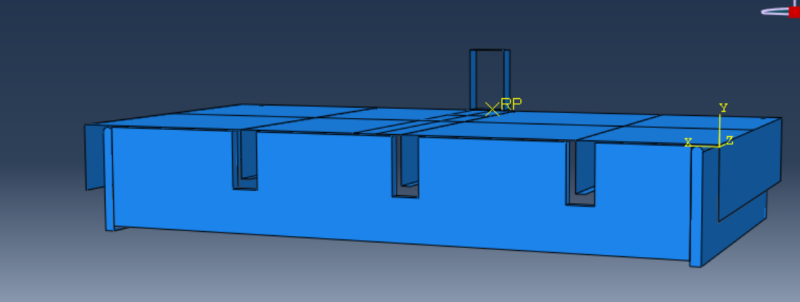
The plate is modelled using S4R elements, while the rig is modelled with C3D8R elements. The nose is discrete rigid.
The General Contact-algorithm is used in the simulations, with some excluded pairs (surface-to-surface between rig/plate and indenter/plate).
The problem I am having (as you can see from the plot below), is that the model is to stiff. I also have a "bump" in curve in the first steps of the analysis. I have made sure that the initial gap between the nose and the plate is sufficient (greater than the shell thicknes) and I have also implemented the smooth step-amplitude. Material properties used in the model are identical to the ones used in the laboratory.
The mesh size and the friction coefficients does not really have that big of an impact on the results.
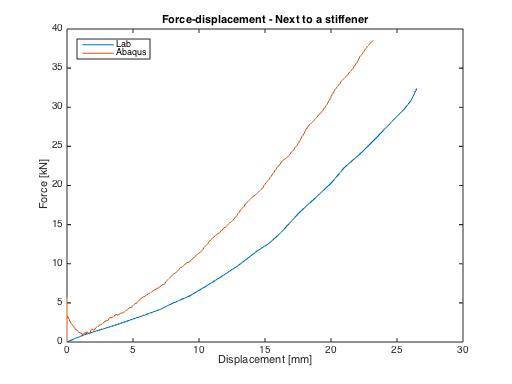
Do you guys have any tips or input on what can be wrong with my model?
Thanks,
Even (Norway)