Nick Melton
New member
In carrying out a repair to an aluminium honeycomb panel, the AC43.13-1B, has the following (Chapter 3, Section 2, Figure 3-11):
"For the repair of larger holes in which it is inconvenient to use a face patch because of aerodynamic smoothness requirements in that area, both the core and facing are sometimes replaced with glass-fibre fabric discs and resin. Undercut the core, as shown in the figure below, in order to obtain a better bonding of the fill with the facing. Fill the core cavity with accurately shaped resin-saturated glass cloth discs and press each ply down to remove any air bubbles. Special care should be taken that the final plies fit well against the underside of the top facing. When the core cavity is filled, close the cut-out in the facing with resin-impregnated glass fibre fabric discs that have been pre-cut to size."
How is this possible to get the plies to fit tightly to the underside of the undercut without using access from the other side? An undercut repair would only be applicable if the cavity was potted?
"For the repair of larger holes in which it is inconvenient to use a face patch because of aerodynamic smoothness requirements in that area, both the core and facing are sometimes replaced with glass-fibre fabric discs and resin. Undercut the core, as shown in the figure below, in order to obtain a better bonding of the fill with the facing. Fill the core cavity with accurately shaped resin-saturated glass cloth discs and press each ply down to remove any air bubbles. Special care should be taken that the final plies fit well against the underside of the top facing. When the core cavity is filled, close the cut-out in the facing with resin-impregnated glass fibre fabric discs that have been pre-cut to size."
How is this possible to get the plies to fit tightly to the underside of the undercut without using access from the other side? An undercut repair would only be applicable if the cavity was potted?
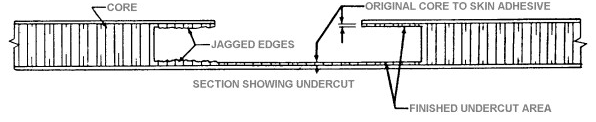