ABrown123
Mechanical
- Jan 31, 2017
- 2
I am designing an induction heating rig to heat a strip on the surface of a steel sample with repeated quenching, through holes in the heating surface of the coil (shown in the third image)
Firstly, could anyone comment on the current coil design (split-return rectangular copper pipe)
Secondly, there are two options for cooling, as shown in the image, one which quenches the sample from the centre leg and one which does so via the centre and return legs. Would the coil get too hot if it was only cooled during the quench cycle (half of the time) as in the second image?
Thanks in advance
Firstly, could anyone comment on the current coil design (split-return rectangular copper pipe)
Secondly, there are two options for cooling, as shown in the image, one which quenches the sample from the centre leg and one which does so via the centre and return legs. Would the coil get too hot if it was only cooled during the quench cycle (half of the time) as in the second image?
Thanks in advance
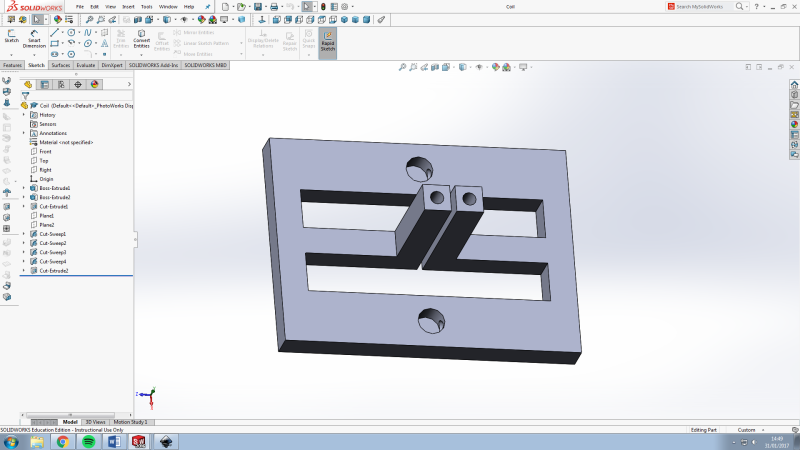

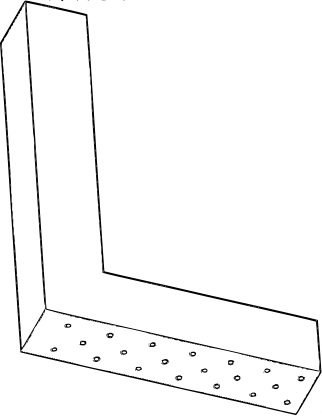
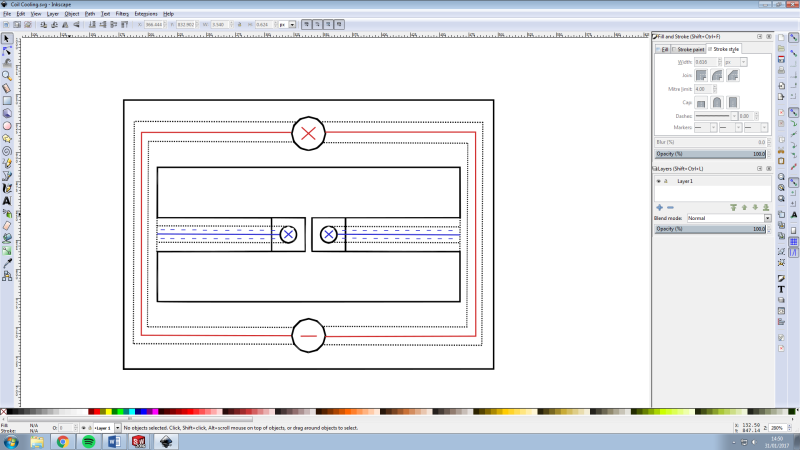
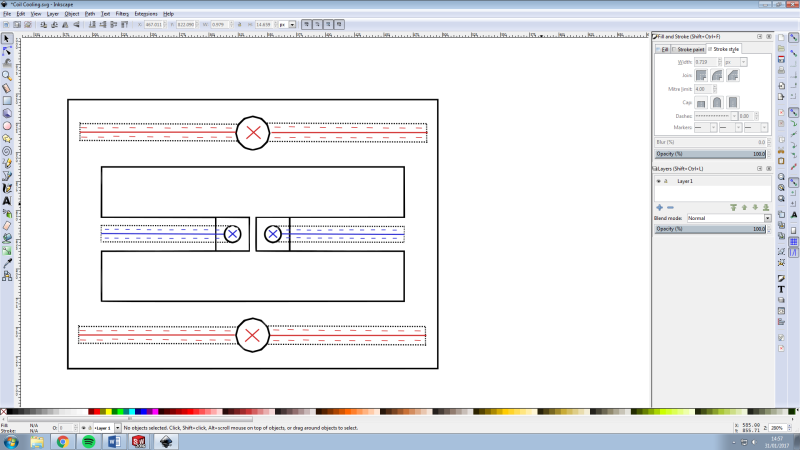