Hi,
I have a unique question on what is the torque on a motor shaft if it is started while already spinning at full speed, but in the opposite direction. The real world case I am trying to analyze is: a pump storage hydro generator (38MVA synchronous machine with a squirrel cage winding on the rotor) is brought up to speed no load (SNL) by the water wheel with no excitation and then connected to the utility system BUT, the system phase rotation is opposite that of the generator. My question is what is the torque that would be produced on the motor/gen shaft?
The machine is a synchronous generator that is designed for induction starting in the pump mode and has a set of shorting bars embedded in the face of the rotor poles (squirrel cage design). Since the machine has no excitation I see this as a 3 phase induction motor and I am using the Torque equation to calculate torque. The equation I am using is:
Where
T=torque
s=slip
E2=rotor voltage
R2=rotor resistance
X2=rotor reactance
Ns=synchronous speed
and
s=(Ns-N)/Ns
Where
N=rotor speed
What I do is I substitute in a negative N into the slip equation, get a slip of 2 and substitute into the Torque eq. Assuming that R & X are small relative to E, that would make the Torque much higher that a locked rotor torque.
I'm not sure if I am doing this right and was hoping that the guru's could chime in.
Note: This will not happen since proper phasing checks will be done first, but the question of what would happen if this were to happen came up.
Thanks,
Bohdan
I have a unique question on what is the torque on a motor shaft if it is started while already spinning at full speed, but in the opposite direction. The real world case I am trying to analyze is: a pump storage hydro generator (38MVA synchronous machine with a squirrel cage winding on the rotor) is brought up to speed no load (SNL) by the water wheel with no excitation and then connected to the utility system BUT, the system phase rotation is opposite that of the generator. My question is what is the torque that would be produced on the motor/gen shaft?
The machine is a synchronous generator that is designed for induction starting in the pump mode and has a set of shorting bars embedded in the face of the rotor poles (squirrel cage design). Since the machine has no excitation I see this as a 3 phase induction motor and I am using the Torque equation to calculate torque. The equation I am using is:
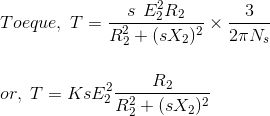
Where
T=torque
s=slip
E2=rotor voltage
R2=rotor resistance
X2=rotor reactance
Ns=synchronous speed
and
s=(Ns-N)/Ns
Where
N=rotor speed
What I do is I substitute in a negative N into the slip equation, get a slip of 2 and substitute into the Torque eq. Assuming that R & X are small relative to E, that would make the Torque much higher that a locked rotor torque.
I'm not sure if I am doing this right and was hoping that the guru's could chime in.
Note: This will not happen since proper phasing checks will be done first, but the question of what would happen if this were to happen came up.
Thanks,
Bohdan