rollingcloud
Aerospace
In the case of self-locking nut. Is it normal to have different definitions across different specs, within the same industry? I am so confused, AS spec should in theory be aligned with GE spec. However, I am not seeing that, am I interpreting it correctly?
AS spec says: Assembly torque is the design torque applied at final assembly. It shall include the net effect of the following:
a. The torque required to overcome kinetic friction between mating bearing faces and between mating threads.
b. The torque required to overcome the self-locking feature.
c. The torque required to apply the desired axial load to a fastener assembly.
The installation torque shall be measured only in the tightening direction. Also: Installation Torque, Tightening Torque.
Seating torque: The torque to bring the bearing surfaces into the seated position, only in the tightening direction.
My thoughts: According to the AS spec, seating torque comes before the assembly torque/installation torque. Seating torque only makes the initial bearing surface contact and does not create the final desired axial load.
In a GE spec, it says a nut is seated when the nut bearing surfaces contacts a spacer and an axial load is induced in the bolt by applying a specified seating torque or by producing a measured extension of the bolt. It also defines maximum installation torque as the highest value obtained as the nut is initially installed on and is being sized by the bolt or the max value obtained during any subsequent on or off cycle.
It says a nut is installed on a bolt when not less than the chamfer plus one-half threads and not more than the chamfer plus 5 threads of the bolt protrude through the nut. Nuts with centralized locking devices do not require the bolt to protrude through the nut provided the bolt passes through the locking device by the chamfer and one and one-half to 5 threads.
My thoughts: According to the GE spec, the installation torque is not related to bearing surface contact, but it's related to the protrusion of the bolt. The GE specs appear to define the seated state the same way as the AS spec's assembled/installed state.
I googled and found the following definition, which aligns with the GE spec, but not the AS spec
AS spec says: Assembly torque is the design torque applied at final assembly. It shall include the net effect of the following:
a. The torque required to overcome kinetic friction between mating bearing faces and between mating threads.
b. The torque required to overcome the self-locking feature.
c. The torque required to apply the desired axial load to a fastener assembly.
The installation torque shall be measured only in the tightening direction. Also: Installation Torque, Tightening Torque.
Seating torque: The torque to bring the bearing surfaces into the seated position, only in the tightening direction.
My thoughts: According to the AS spec, seating torque comes before the assembly torque/installation torque. Seating torque only makes the initial bearing surface contact and does not create the final desired axial load.
In a GE spec, it says a nut is seated when the nut bearing surfaces contacts a spacer and an axial load is induced in the bolt by applying a specified seating torque or by producing a measured extension of the bolt. It also defines maximum installation torque as the highest value obtained as the nut is initially installed on and is being sized by the bolt or the max value obtained during any subsequent on or off cycle.
It says a nut is installed on a bolt when not less than the chamfer plus one-half threads and not more than the chamfer plus 5 threads of the bolt protrude through the nut. Nuts with centralized locking devices do not require the bolt to protrude through the nut provided the bolt passes through the locking device by the chamfer and one and one-half to 5 threads.
My thoughts: According to the GE spec, the installation torque is not related to bearing surface contact, but it's related to the protrusion of the bolt. The GE specs appear to define the seated state the same way as the AS spec's assembled/installed state.
I googled and found the following definition, which aligns with the GE spec, but not the AS spec
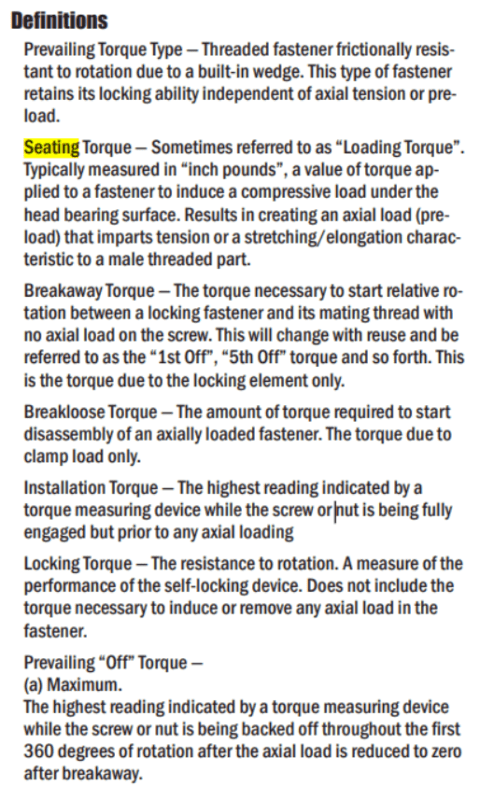