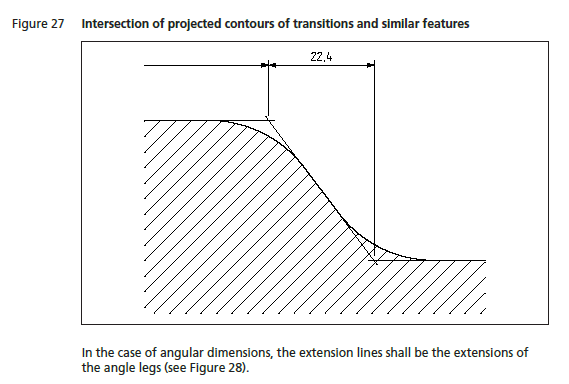
Just following on from the previous thread, I can understand why you would use an Intersect Dimension for a feature such as the upper radius in the figure, as this is where there will be material before the radius has been machined. I don't understand why you would use an intersect for the lower dimension as this material, which the intersecting lines would theoretically remove is used, rather than perhaps showing and dimensioning the Centre mark of that radius.
I just want to clear up that this is a standard way to dimension this "Internal" radius or if it would be clearer using the centre point.
Thanks