am working in a power station recently commissioned.It has a 500KV switchyard which is an extension of the existing one.Now attached pictures show quality of installation.We are pressing on the contractor that the irregular bending of the bus bar is not onle aesthetically bad but also the bending will cause the thickness of the tube to be less at the bends effecting its current carrying capacity.Can any one has more points to add to. Three pictures are attached.Two
of new one and one of old switchyard
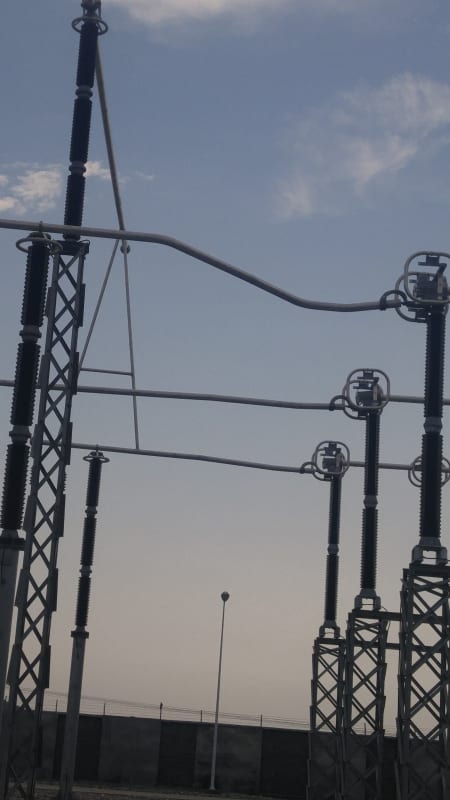
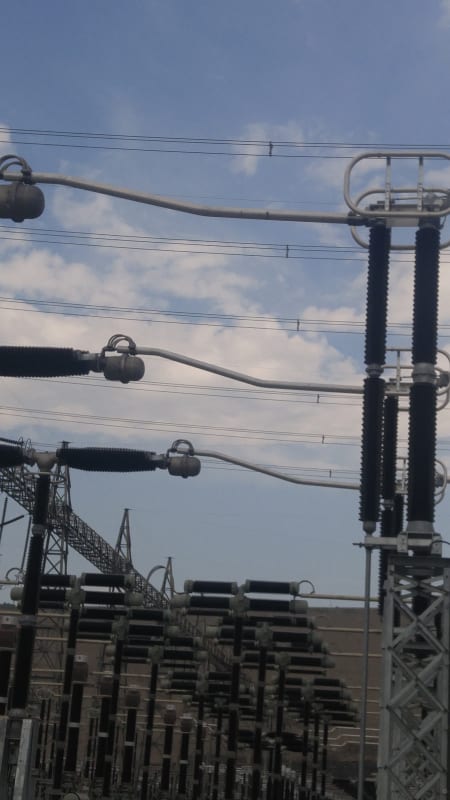
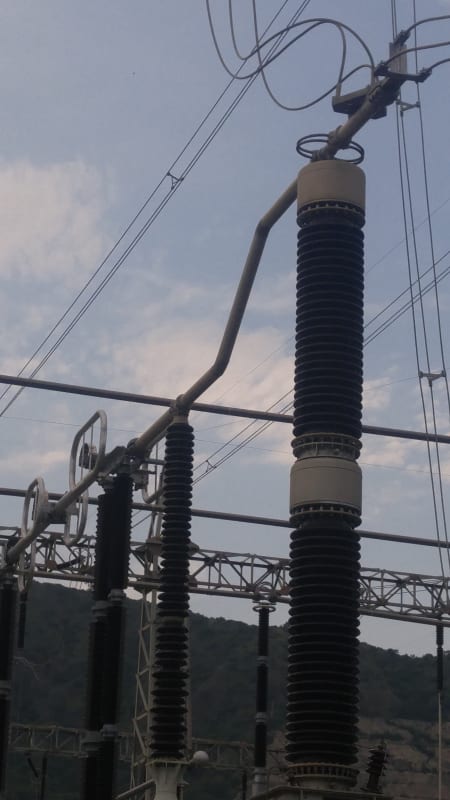