JohnStarling
Mechanical
Hi,
I have a part (a bracket I think is the best word in english to describe this part), which has two nominaly coaxial holes in it (please see the attachment). The holes are of the same diameter. I want to state that these two holes (Ø 35 H9) should be machined with one operation (for example G76 fineboring cycle), to a achieve good coaxility of the holes (a precision pin will go trough the holes).
I have uesd coaxility geo. tolerance (acc to ISO 1101) to make it work. But I have some questions.
1) On the drawing I set the axis of one hole (see annotation #2) as a base and the I attach the coaxility feature control frame to the axis of second hole. But beacause the holes have the same diameter, there is no point to show the diameter of the second hole again. So I use a blank diameter dimension line just to attach the coaxility tolerance (see annotation #1). Can I do this?
2) Is this kind of approach unabmiguous or can it be better done with some other tolerance (in ISO system)?
Best regards,
JS
I have a part (a bracket I think is the best word in english to describe this part), which has two nominaly coaxial holes in it (please see the attachment). The holes are of the same diameter. I want to state that these two holes (Ø 35 H9) should be machined with one operation (for example G76 fineboring cycle), to a achieve good coaxility of the holes (a precision pin will go trough the holes).
I have uesd coaxility geo. tolerance (acc to ISO 1101) to make it work. But I have some questions.
1) On the drawing I set the axis of one hole (see annotation #2) as a base and the I attach the coaxility feature control frame to the axis of second hole. But beacause the holes have the same diameter, there is no point to show the diameter of the second hole again. So I use a blank diameter dimension line just to attach the coaxility tolerance (see annotation #1). Can I do this?
2) Is this kind of approach unabmiguous or can it be better done with some other tolerance (in ISO system)?
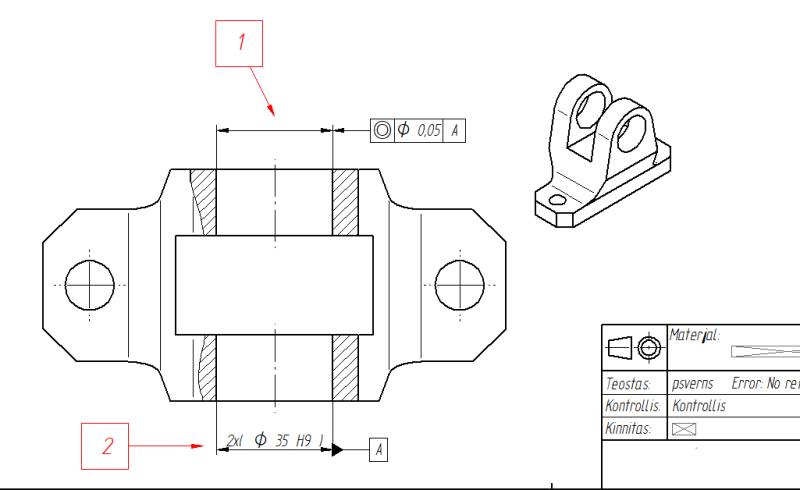
Best regards,
JS