Hello,
I had almost a final design (1.xt, added to this post) and suddenly there was a need to use other castors with another (bigger) interface.
The new castor interface is very big, and from using only 1 screw I had to use 4 screws.
The Item profile end couldn't connect to the new castor and if I use a base plate between the castor and the profile end, the base plate will only be partially supported - looks bad.
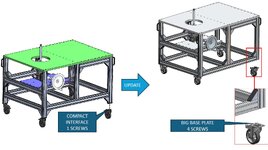
As a result I changed the design a little bit (2.xt, added to this post) and I lowered the lower beams to the minimum possible height.
The motivation was to support the new castor interface base almost fully (there is still an area that isn't supported) supported by the Item profiles.
I think the construction in this design isn't quite good as the former design... what do you think? is there any other elegant solution that will prevent changing my original design?
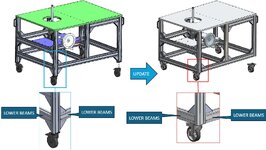
I had almost a final design (1.xt, added to this post) and suddenly there was a need to use other castors with another (bigger) interface.
The new castor interface is very big, and from using only 1 screw I had to use 4 screws.
The Item profile end couldn't connect to the new castor and if I use a base plate between the castor and the profile end, the base plate will only be partially supported - looks bad.
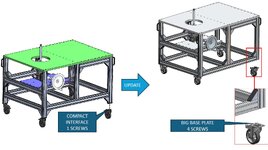
As a result I changed the design a little bit (2.xt, added to this post) and I lowered the lower beams to the minimum possible height.
The motivation was to support the new castor interface base almost fully (there is still an area that isn't supported) supported by the Item profiles.
I think the construction in this design isn't quite good as the former design... what do you think? is there any other elegant solution that will prevent changing my original design?
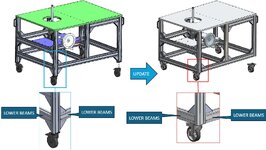
Attachments
Last edited: