Temporaryworks
Structural
Hi,
I am a structural engineer designing a rail buffer stop to resist a force of 200kN @ 10kmph. The buffer stop works by small clamps at the bottom which are tensioned against the rail shoe to provide a known force (see attached sketch for an example). This known force can then be used to calculate the frictional force required to overcome the inertia i.e. static friction - this is very important for my structural steel design as this will determine the greatest force that will be applied to the structure.
At the point of sliding, the clamp will move with the train and dissipate the energy along the rail. The kinetic friction then takes over and the train strike energy gets dissapated as the clamp slides to a stop. I need to calculate the kinetic frictional co-efficient here because this will determine the distance over which it takes the train to stop after it has started sliding.
This is where I get a bit lost and am looking for help - how do I calulcate this kinetic friction reistance, plus the friction resistance would never be constant as the train is decelerating. My head is spinning - any advice?
Thanks in advance.
I am a structural engineer designing a rail buffer stop to resist a force of 200kN @ 10kmph. The buffer stop works by small clamps at the bottom which are tensioned against the rail shoe to provide a known force (see attached sketch for an example). This known force can then be used to calculate the frictional force required to overcome the inertia i.e. static friction - this is very important for my structural steel design as this will determine the greatest force that will be applied to the structure.
At the point of sliding, the clamp will move with the train and dissipate the energy along the rail. The kinetic friction then takes over and the train strike energy gets dissapated as the clamp slides to a stop. I need to calculate the kinetic frictional co-efficient here because this will determine the distance over which it takes the train to stop after it has started sliding.
This is where I get a bit lost and am looking for help - how do I calulcate this kinetic friction reistance, plus the friction resistance would never be constant as the train is decelerating. My head is spinning - any advice?
Thanks in advance.
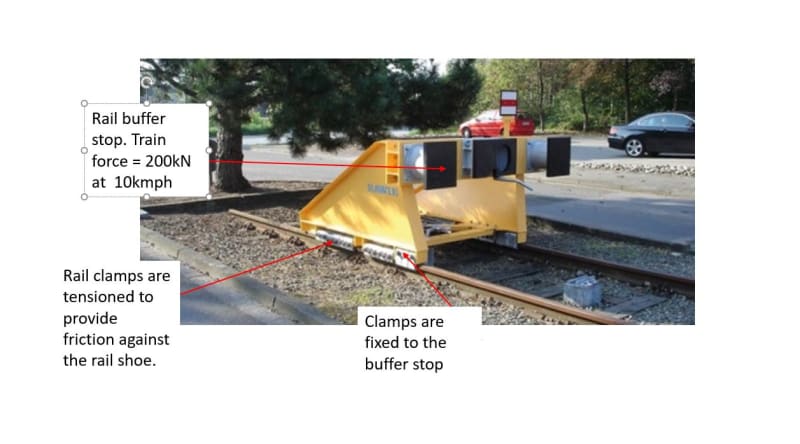