RFreund
Structural
- Aug 14, 2010
- 1,885
I'm trying to get some feedback on built-up angle joints. For some reason I just don't like the look of these. It doesn't seem like you will develop the full capacity of the steel before cracking of the joint, but hopefully I am wrong. Below are some welded joint details for built-up angles where the joint is in bending.
Are these more or less what you would use to achieve a full penn weld at the joint in order to use the full yield strength of the plate?
EIT
Are these more or less what you would use to achieve a full penn weld at the joint in order to use the full yield strength of the plate?
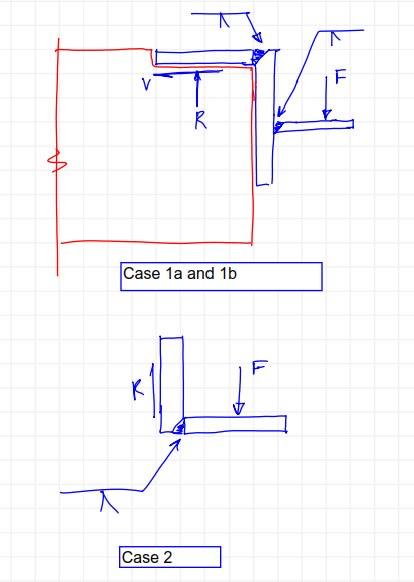
EIT