BEMPE16524
Mechanical
Hello guys, i have tried to figure out why do they make the base unparallel as in the photo (you can see the hydraulic cylinders as well) but can't think off anything logical.
appreciate all ideas.
R.Efendy
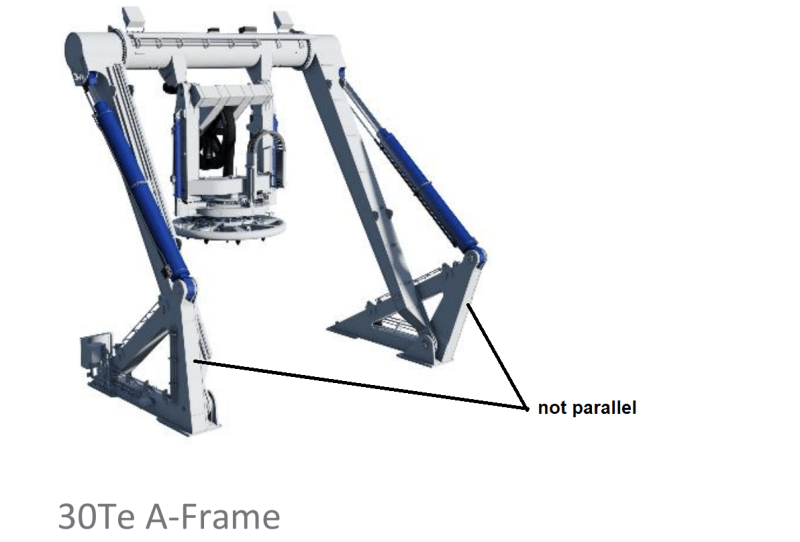
appreciate all ideas.
R.Efendy