adrich91
Chemical
- Oct 6, 2024
- 10
Good evening, everyone,
I'm back here again for further enlightenment (greatly appreciated
)
I was reviewing the subject of pumping liquids and I had understood that at the exit of the pipe to the atmosphere (for example a tap or end of open pipe) the pressure was always the atmospheric pressure; However, I have been reviewing a website and it has brought me many doubts and I need someone to help me understand.
I have been misled by the attached drawing (which says that at the tap outlet there is 3 bar g, when I think it would be 0 bar g):
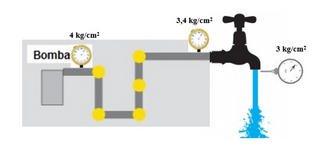
If I pump from a tank that is open to the atmosphere, and I have to circumvent a circuit with a pressure loss X, I understand that I make the calculations saying the flow that I want to move and that at the end of line I have 0 bar g and after that the software (aspen hysys, for example) calculates the power of the pump and the pressure at the discharge of the pump.
If I want more flow, I will have to have more discharge pressure and the pressure drop will be higher, but I will always have atmospheric pressure at the end of the line, right?
Thank you! and sorry for my english!
I'm back here again for further enlightenment (greatly appreciated
I was reviewing the subject of pumping liquids and I had understood that at the exit of the pipe to the atmosphere (for example a tap or end of open pipe) the pressure was always the atmospheric pressure; However, I have been reviewing a website and it has brought me many doubts and I need someone to help me understand.
I have been misled by the attached drawing (which says that at the tap outlet there is 3 bar g, when I think it would be 0 bar g):
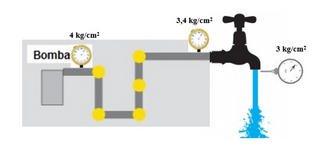
If I pump from a tank that is open to the atmosphere, and I have to circumvent a circuit with a pressure loss X, I understand that I make the calculations saying the flow that I want to move and that at the end of line I have 0 bar g and after that the software (aspen hysys, for example) calculates the power of the pump and the pressure at the discharge of the pump.
If I want more flow, I will have to have more discharge pressure and the pressure drop will be higher, but I will always have atmospheric pressure at the end of the line, right?
Thank you! and sorry for my english!