Hi everyone,
I have a notched part which I pull apart to create a crack. For the crack, I use XFEM and it works well. However, when I try to extract the load-displacement data, I only get a straight line. The crack is clearly initiated and growing, which means that the load should decrease, e.g. the line should drop and not increase further (I have displacement control). To plot the load-displacement data, I created a set of nodes on either side of the specimen which I constrained to a reference point. The right reference point is fixed, the left one moves further to the left.
Any help is greatly appreciated, thanks so much!
P.S. I also attached the .cae and .jnl files.
I have a notched part which I pull apart to create a crack. For the crack, I use XFEM and it works well. However, when I try to extract the load-displacement data, I only get a straight line. The crack is clearly initiated and growing, which means that the load should decrease, e.g. the line should drop and not increase further (I have displacement control). To plot the load-displacement data, I created a set of nodes on either side of the specimen which I constrained to a reference point. The right reference point is fixed, the left one moves further to the left.
Any help is greatly appreciated, thanks so much!
P.S. I also attached the .cae and .jnl files.
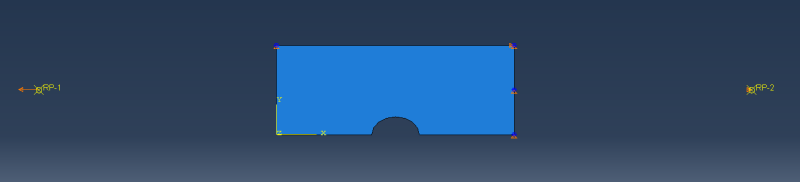
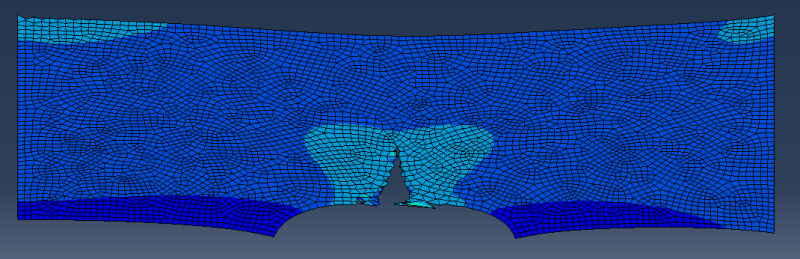
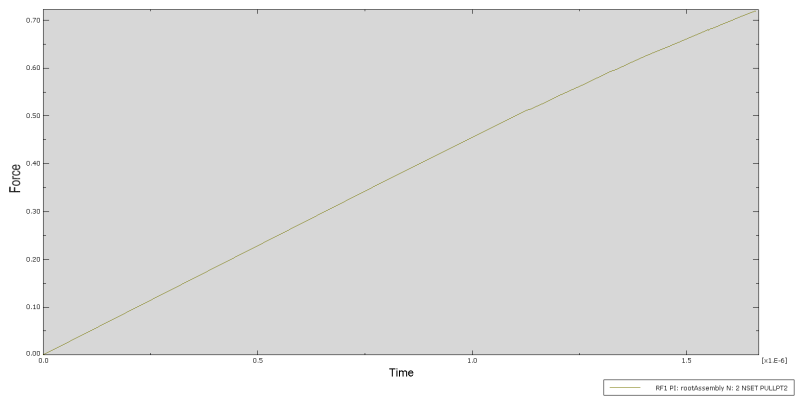