Peter the Engineer
Mechanical
Hi, I am fairly new to GD&T and still learning from the 2009 GD&T standard book. I noticed that if an ID or OD is used as a secondary datum feature, it is usually not given a location tolerance. Only perpendicularity tolerance is used.
Fig 4-9 and 4-15 from the standard illustrate this. The secondary datum features are only given perpendicularity controls. That being said, are we not controlling the position of these secondary datum features? Are we saying that these secondary datum features are free to float anywhere, just as long as other features that are dependent on them are located based on their actual locations? I am always under the impression that for any given feature, we have to control the location, orientation, form, and size. Thanks masters!
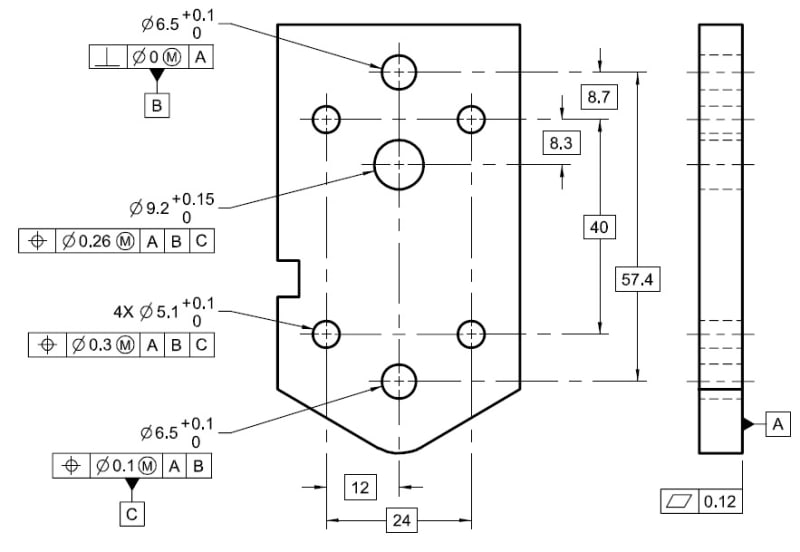
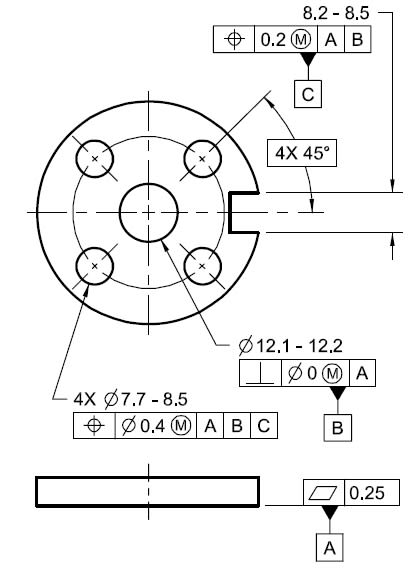
Fig 4-9 and 4-15 from the standard illustrate this. The secondary datum features are only given perpendicularity controls. That being said, are we not controlling the position of these secondary datum features? Are we saying that these secondary datum features are free to float anywhere, just as long as other features that are dependent on them are located based on their actual locations? I am always under the impression that for any given feature, we have to control the location, orientation, form, and size. Thanks masters!