aleemullah
Materials
Hi Guys,
I work at a coal fired power plant as a maintenance engineer and lately we have been facing the issue of boiler reheater tubes cracking at bends. I have attached couple of pictures of last two events. One tube had the crack on the side of bent surface, while other on the outside of bent surface.
This appears to be lip fracture (fish mouth?). I have suggested to perform hardness and metallography of the affected tubes. Will that be helpful?
Any help will be appreciated in helping us solve the problem as this is causing forced outages at our plant.
Regards,
Aleem
I work at a coal fired power plant as a maintenance engineer and lately we have been facing the issue of boiler reheater tubes cracking at bends. I have attached couple of pictures of last two events. One tube had the crack on the side of bent surface, while other on the outside of bent surface.
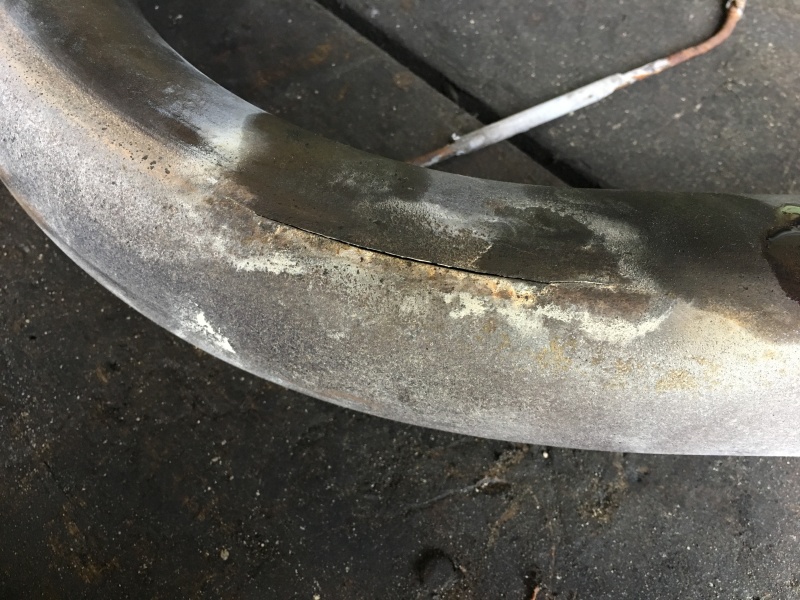
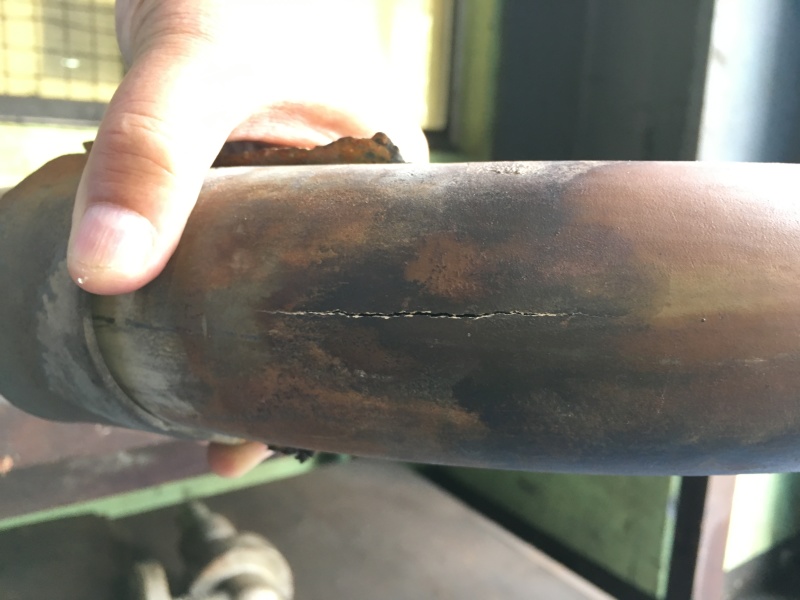
This appears to be lip fracture (fish mouth?). I have suggested to perform hardness and metallography of the affected tubes. Will that be helpful?
Any help will be appreciated in helping us solve the problem as this is causing forced outages at our plant.
Regards,
Aleem