I can't figure out where to post this so here it is.
I've got a machine that has a cantilevered two inch diameter axle six feet long. To support its load at a couple hundred RPM it needs to have BOTH ends supported. But to unload the product one end needs to have all support on one end go away frequently.
To do this they use a pneumatic cylinder to drive the support arm thru about 90°.
This is a looking 'straight down' view.
The problem is that this nasty arm is about 16 inches long and so sweeps a pretty substantial area. You don't want anyone or thing to be in the swept area when it does its thing.
Currently they have an optical retroreflector light beam switch that looks parallel to the closed (engaged) arm at a corner reflector screwed to the wall. If it's blocked the arm can't swing.
This is lousy because someone can safely be standing there well out of the arm's path and the process can be blocked causing confusion. Furthermore the arm sweeps over a table surface. Stuff can be placed there that isn't seen by the 2mm light beam with predicted results. Also someone can actually stand to the right just far enough to still get batted on the sweep though unseen by the beam.
In a perfect world I'd love some sort of light curtain that would flesh-out the entire swept area in 2D and yea or nae the cycle.
In a less than perfect world I'd like something to do at least a better job than one tiny beam path at protecting people. A straight look-down could be a problem because the operator is all over above the arm during product unloading and blank loading.
There could be something -not too heavy- four feet above the arm on a support?
Let's see what you've got.
Keith Cress
kcress -
I've got a machine that has a cantilevered two inch diameter axle six feet long. To support its load at a couple hundred RPM it needs to have BOTH ends supported. But to unload the product one end needs to have all support on one end go away frequently.
To do this they use a pneumatic cylinder to drive the support arm thru about 90°.
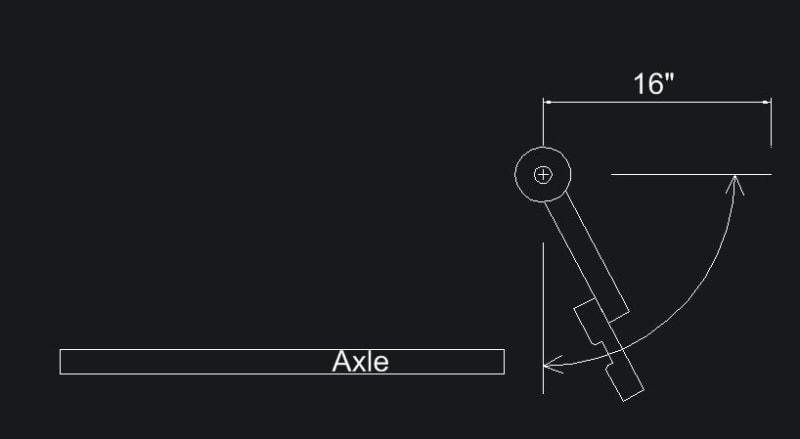
This is a looking 'straight down' view.
The problem is that this nasty arm is about 16 inches long and so sweeps a pretty substantial area. You don't want anyone or thing to be in the swept area when it does its thing.
Currently they have an optical retroreflector light beam switch that looks parallel to the closed (engaged) arm at a corner reflector screwed to the wall. If it's blocked the arm can't swing.
This is lousy because someone can safely be standing there well out of the arm's path and the process can be blocked causing confusion. Furthermore the arm sweeps over a table surface. Stuff can be placed there that isn't seen by the 2mm light beam with predicted results. Also someone can actually stand to the right just far enough to still get batted on the sweep though unseen by the beam.
In a perfect world I'd love some sort of light curtain that would flesh-out the entire swept area in 2D and yea or nae the cycle.
In a less than perfect world I'd like something to do at least a better job than one tiny beam path at protecting people. A straight look-down could be a problem because the operator is all over above the arm during product unloading and blank loading.
There could be something -not too heavy- four feet above the arm on a support?
Let's see what you've got.
Keith Cress
kcress -