MattNCSU03
Mechanical
I'm designing a fluids test loop in a laboratory and need to design and have fabricated a short pipe spool with flanged ends. I initially modeled something with a WN flanges and a short section of pipe but because I needed to fit in half a dozen instrument taps and a NPT branch connection within a short overall length, I thought it would be much easier to machine something from a bar. We're also concerned with weld distortion to the inner bore from welding all the bosses required.
Spool Description:
Side 1: 4" Class 150 flat-faced flange
Side 2: 6" Class 150 flat-faced flange
bore: 4.03"
branch 1: 2" NPT
branch 2: 3/8" NPT (drain)
Misc: 6x 5/8" instrument ports around circumference (2 as close to side 1 as practicable and 4 as close to side 2)
Nominal thickness: 0.75" (set at so instruments can sit on a flat machined into the OD vs on a boss)
Overall length: 9.5"
Design conditions: water @ <100 psi / < 100°F
older preview image (hasn't been updated to reflect smaller side 1 flange):
Our pressure safety board prefers test loops and components to be designed to an ASME code, BPVC and B31.1, 31.3, or 31.9 when possible. This loop is low enough pressure/temp I could use 31.9 per our rules.
With an eye to making the above spool code compliant, it looks like I could have it rough forged and then final machined to meet B16.5 (not sure about meeting 6.12.6 for auxiliary port size, depends on what "unless otherwise specified" means..e.g. by the code or user) or fully machined from a bar by using BPVC VIII.1 UG-14(b)(4). Am I missing something or making this overly complicated?
Thanks in advance for the advice!
Matt
Spool Description:
Side 1: 4" Class 150 flat-faced flange
Side 2: 6" Class 150 flat-faced flange
bore: 4.03"
branch 1: 2" NPT
branch 2: 3/8" NPT (drain)
Misc: 6x 5/8" instrument ports around circumference (2 as close to side 1 as practicable and 4 as close to side 2)
Nominal thickness: 0.75" (set at so instruments can sit on a flat machined into the OD vs on a boss)
Overall length: 9.5"
Design conditions: water @ <100 psi / < 100°F
older preview image (hasn't been updated to reflect smaller side 1 flange):
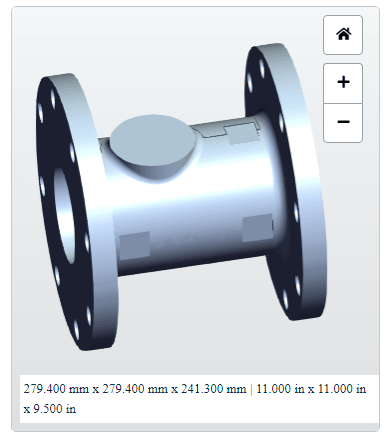
Our pressure safety board prefers test loops and components to be designed to an ASME code, BPVC and B31.1, 31.3, or 31.9 when possible. This loop is low enough pressure/temp I could use 31.9 per our rules.
With an eye to making the above spool code compliant, it looks like I could have it rough forged and then final machined to meet B16.5 (not sure about meeting 6.12.6 for auxiliary port size, depends on what "unless otherwise specified" means..e.g. by the code or user) or fully machined from a bar by using BPVC VIII.1 UG-14(b)(4). Am I missing something or making this overly complicated?
Thanks in advance for the advice!
Matt