BiPolarMoment
Mechanical
So, we have some machined parts of somewhat dubious history where the drawings indicate the parts are 316L but due to the fact one of the components exhibited ferromagnetism and was not galling in a same-material pair, we suspected the material may actually be hardened 400 series (e.g. 416/420) but simply did not have that correctly documented. Fast-forward to one metallurgical test later and it confirmed that the suspect material did meet UNS S31603 (hardness 86 HRB).
So the main question is: If the magnetism was present from the raw form (due to condition furnished?), would that be associated with any appreciable/expected galling resistance when mated against another 316L item?
History: we have some equipment that has been in use for >10 years and the major 'functioning' component of interest is a ~5/16" cylindrical post that is rotated a few times (loosely mated) within a bore in the part in question (e.g. 2-3 turns and is then held in that position by a ratchet/pawl mechanism)--there is a side load on this post applied above the 'joint' while it's being turned that increases to ~10lbf . Galling has not been an issue in the equipment presently in use to my knowledge.
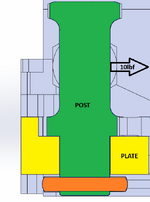
While we were attempting to make design 'improvements' on a new purchase, efforts were made to minimize the number of changes to try to avoid issues such as what we are experiencing (lol), but nevertheless several changes did occur and perhaps are the contributing factors. For example: the post/bore clearance was reduced (still a clearance fit) to limit 'rattling'; the ratchet/pawl mechanism (not shown) was made more robust which incidentally applies it's own lateral force on the post ('Into' the view, near the interface of the components) not indignificant, but not quantified; it's likely the surface finishes for all components are not identical (and were never well defined). Suffice to say that once we began testing this new iteration of the equipment, galling occurred at this interface almost immediately which has halted implementation plans while we investigate.
It was perhaps 'hoped' that because these other changes were considered/thought to be inconsequential that the raw material of the 'magnetic' component may have been the solution/problem. Now we are not so sure.
So the main question is: If the magnetism was present from the raw form (due to condition furnished?), would that be associated with any appreciable/expected galling resistance when mated against another 316L item?
History: we have some equipment that has been in use for >10 years and the major 'functioning' component of interest is a ~5/16" cylindrical post that is rotated a few times (loosely mated) within a bore in the part in question (e.g. 2-3 turns and is then held in that position by a ratchet/pawl mechanism)--there is a side load on this post applied above the 'joint' while it's being turned that increases to ~10lbf . Galling has not been an issue in the equipment presently in use to my knowledge.
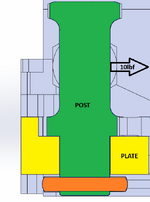
While we were attempting to make design 'improvements' on a new purchase, efforts were made to minimize the number of changes to try to avoid issues such as what we are experiencing (lol), but nevertheless several changes did occur and perhaps are the contributing factors. For example: the post/bore clearance was reduced (still a clearance fit) to limit 'rattling'; the ratchet/pawl mechanism (not shown) was made more robust which incidentally applies it's own lateral force on the post ('Into' the view, near the interface of the components) not indignificant, but not quantified; it's likely the surface finishes for all components are not identical (and were never well defined). Suffice to say that once we began testing this new iteration of the equipment, galling occurred at this interface almost immediately which has halted implementation plans while we investigate.
It was perhaps 'hoped' that because these other changes were considered/thought to be inconsequential that the raw material of the 'magnetic' component may have been the solution/problem. Now we are not so sure.