I am using Mechanical APDL to create load cases. I have several load cases (8) that I would like to perform a set of comparisons on. The lcoper command says that the operators min/max/abmn/abmx
Does anyone here know exactly how this is done? I understand that the lcoper operations are performed at the component level (as set by the sumtype command) in the solution coordinate system. First, I don't know exactly what variable (stress, displacement, force, etc) is used for performing this comparison. Second, I don't understand how the maximum of a tensor (for stress) or vector (for displacement or force) can be taken, unless the comparison is done solely at the component level. But does that mean that the min/max/abmn/abmx of each component is calculated and stored? And if the comparison is done with the stresses, then how is the displacements determined? Or vice versa? Regardless, are the results physically meaningful if the component stresses are a mishmash of two load cases (or in my case, the mishmash of 8 load cases?
The reason that I ask is that when I perform such am operation, the displacement field is discontinuous (my cylinder looks like about a third of it is offset, with the connecting elements being stretched). See below.
Compare and save in database the (algebraic minimum)(algebraic maximum)(absolute minimum)(absolute maximum) of database and LCASE1.
Does anyone here know exactly how this is done? I understand that the lcoper operations are performed at the component level (as set by the sumtype command) in the solution coordinate system. First, I don't know exactly what variable (stress, displacement, force, etc) is used for performing this comparison. Second, I don't understand how the maximum of a tensor (for stress) or vector (for displacement or force) can be taken, unless the comparison is done solely at the component level. But does that mean that the min/max/abmn/abmx of each component is calculated and stored? And if the comparison is done with the stresses, then how is the displacements determined? Or vice versa? Regardless, are the results physically meaningful if the component stresses are a mishmash of two load cases (or in my case, the mishmash of 8 load cases?
The reason that I ask is that when I perform such am operation, the displacement field is discontinuous (my cylinder looks like about a third of it is offset, with the connecting elements being stretched). See below.
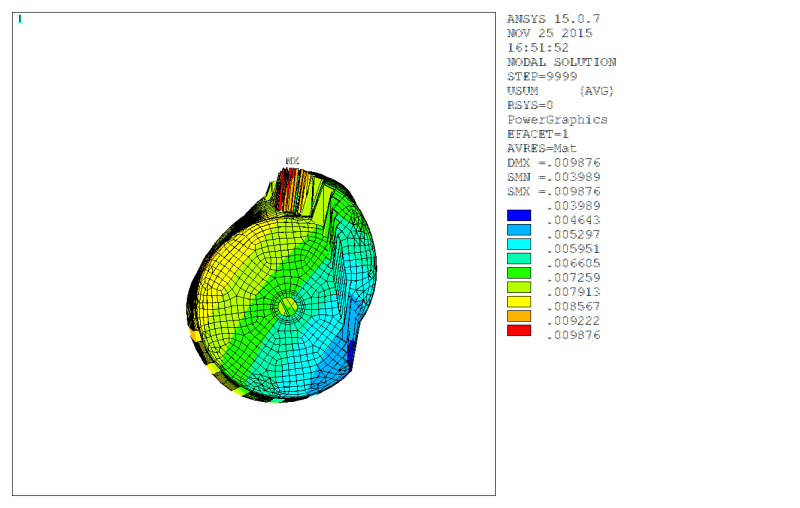