Logan82
Structural
- May 5, 2021
- 212
Hi!
Is there a requirement in a standard specifying that the max size of a filled weld = the thickness of the smallest plate?
For instance, in this case, would the max size of the fillet weld be 12 mm?
Also, could it be possible to have 2 fillet welds of 12 mm on a plate of 12 mm?
Is there a requirement in a standard specifying that the max size of a filled weld = the thickness of the smallest plate?
For instance, in this case, would the max size of the fillet weld be 12 mm?
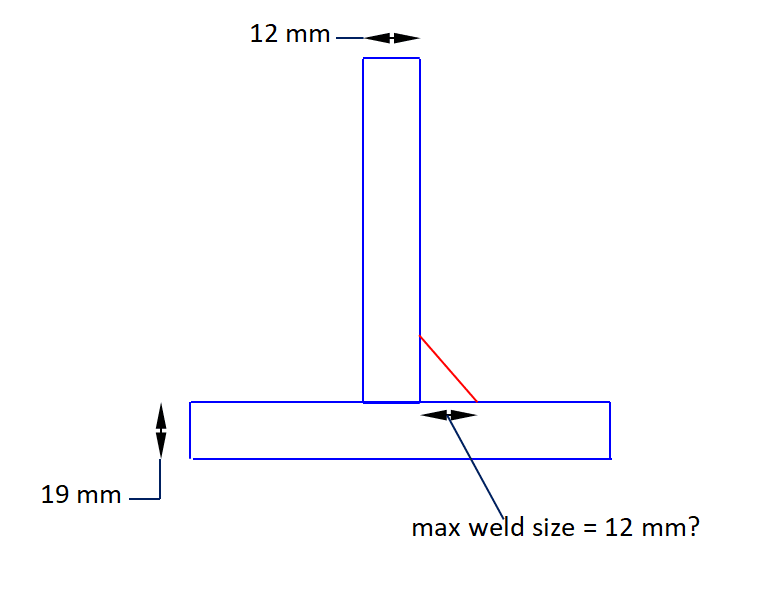
Also, could it be possible to have 2 fillet welds of 12 mm on a plate of 12 mm?
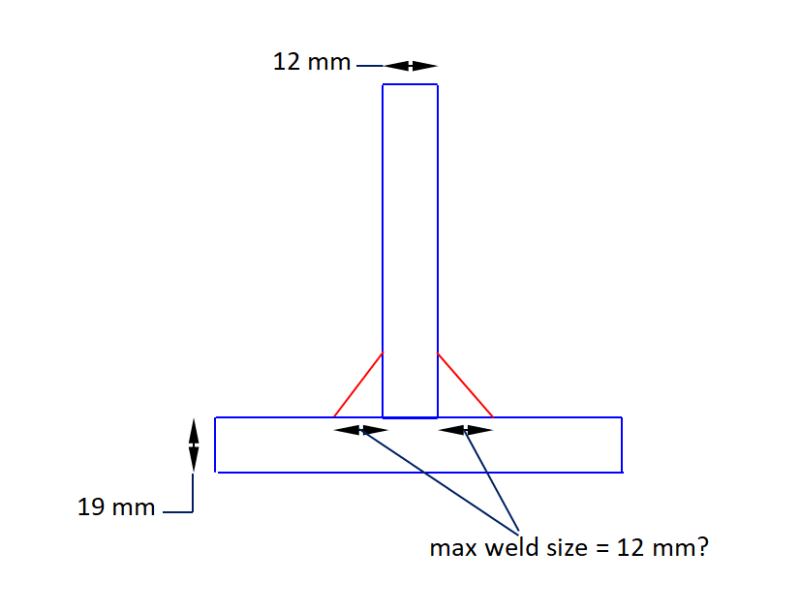