DistressedNerd
Electrical
Hello - I've been thinking about a seemingly simple problem for days with no avail. Even the sheet metal "unfolding" software to create a flat pattern from curved shapes fails because it cannot take into account the manufacturing method (manual metal twister). Yes, I know a flight screw can be created with a cold rolling machine, but I would like to produce it with what I have. If you can come up with a solution backed with evidence you are beyond my MIT grad cognitive abilities. Thank you in advance you to those geniuses out there. Please see image.
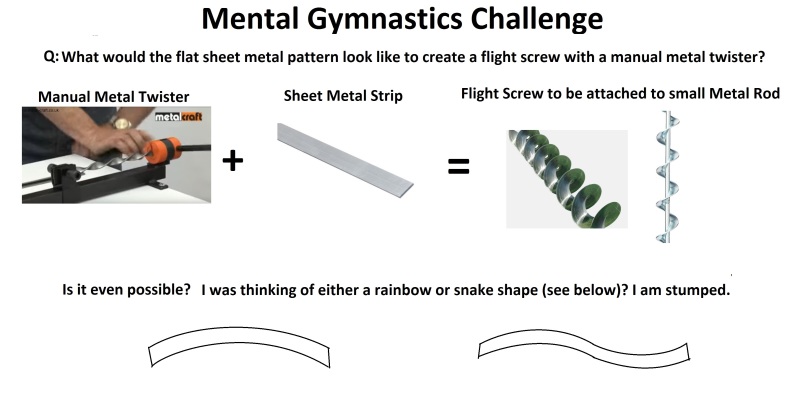