MegaStructures
Structural
- Sep 26, 2019
- 376
Hello all,
I would like to make sure I am not unintentionally introducing errors into my model by gluing non coincident hex meshes as below. I understand 'gluing' surfaces adds rigid elements to connect the nodes of the touching elements, which is why I have moved my glue point away from my anticipated stress concentration at the radius of the transition. Is there any issue with this setup?
Alternatively I can cut this object in 4 pieces, mesh a surface, and revolve the elements, but that results in over a million elements, where this method results in ~200,000.
I would like to make sure I am not unintentionally introducing errors into my model by gluing non coincident hex meshes as below. I understand 'gluing' surfaces adds rigid elements to connect the nodes of the touching elements, which is why I have moved my glue point away from my anticipated stress concentration at the radius of the transition. Is there any issue with this setup?
Alternatively I can cut this object in 4 pieces, mesh a surface, and revolve the elements, but that results in over a million elements, where this method results in ~200,000.
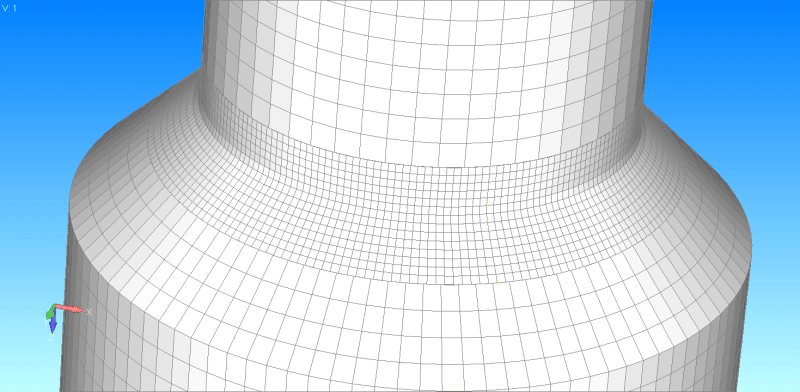