Pavan Kumar
Chemical
- Aug 27, 2019
- 367
Hi All,
I am trying to fix the maximum operating pressure of Steam piping downstream of a Control Valve. The Upstream pressure is 12 bar(g) with saturated steam. The downstream pressure needs to be fixed so that the users in the network get at least 5 bar(g) pressure. I performed a flow model and got that with a operating pressure (pressure downstream of the control valve) of 6.3 bar(g) the users can get at least 5.3 bar(g). There is a PSV downstream of the control valve which is set at 7 bar(g). The design pressure of the downstream piping is 10 bar(g). For some reason they donot want to set the PSV at 10 bar(g). I saw some posts which says the maximum differential between PSV Set pressure and maximum operating pressure is the larger of 10% of PSV set pressure or 25 psi. The PSV will be conventional type.
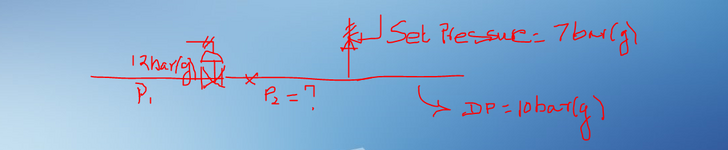
In my case, 10% of PSV Set Pressure = 0.10*7*14.5=10.15 psi, so I should use 25 psi differential which means my maximum operating pressure would be 5.27 bar(g) = [(7*14.5-25)/14.5]. This is too low as the farthest user will now only get 4.3 bar(g). I really cannot go 6 bar(g) operating pressure. I want some expert guidance and reference to code if possible in this problem.
https://www.cheresources.com/invision/topic/2581-psvoperating-pressuremawp/
Thanks and Regards,
Pavan Kumar
I am trying to fix the maximum operating pressure of Steam piping downstream of a Control Valve. The Upstream pressure is 12 bar(g) with saturated steam. The downstream pressure needs to be fixed so that the users in the network get at least 5 bar(g) pressure. I performed a flow model and got that with a operating pressure (pressure downstream of the control valve) of 6.3 bar(g) the users can get at least 5.3 bar(g). There is a PSV downstream of the control valve which is set at 7 bar(g). The design pressure of the downstream piping is 10 bar(g). For some reason they donot want to set the PSV at 10 bar(g). I saw some posts which says the maximum differential between PSV Set pressure and maximum operating pressure is the larger of 10% of PSV set pressure or 25 psi. The PSV will be conventional type.
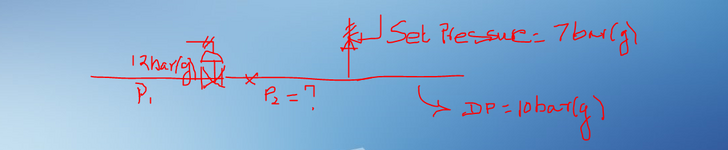
In my case, 10% of PSV Set Pressure = 0.10*7*14.5=10.15 psi, so I should use 25 psi differential which means my maximum operating pressure would be 5.27 bar(g) = [(7*14.5-25)/14.5]. This is too low as the farthest user will now only get 4.3 bar(g). I really cannot go 6 bar(g) operating pressure. I want some expert guidance and reference to code if possible in this problem.
https://www.cheresources.com/invision/topic/2581-psvoperating-pressuremawp/
Thanks and Regards,
Pavan Kumar