bryansonnier
Mechanical
- Dec 20, 2011
- 80
I'm having trouble modeling this in excel so i'm sure i'm not getting the equations right. Most of what i have is all linear for instance force pushing the needle up (see image for reference) I have as P1*A1-P2*A1-P3*A2-k*x where the x is 0-1 and it is correlated to the Cv of the needle and seat i have ranging from cv=10 (practically no differential) to cv=.28 (about 5,000 psi differential). P3 is 0 going back to tank. P2 is dependent on the Cv. For simplicity i'm using water and simple cv calculation of Cv=Q(SG/deltaP)1/2. P1 and P2 are being fed from a manual needle and seat holding pressure against a positive displacement pump.
Modeling the single drop is simply application of the Cv equation P1=(Q/Cv)2*SG+P2. However when i try to model the second part i end up with a whole bunch of nothing until the P1 hits 5000 and then the Cv of the second part goes which has gone from 10 to 2 in a gradual form goes to .28 in like 1 step (At this point on manual section i'm incrementing Cv by 0.001 per step, so 0.301, 0.300, 0.299.... etc. I'm using a k of 5000 at 1" for the spring. Please see attached spread sheet for rough idea of where i'm at.
For the second Cv i tried to interpolate it from the range deltaP1-2 0-5000, Cv 10-.28 with .28 being the point at which the spring would be fully compressed and maximum desired drop achieved. I'm trying to model this with some degree of accuracy so i don't have to spend thousands and thousands experimenting with different spring strengths and chamber diameters.
Excel File
Image
Modeling the single drop is simply application of the Cv equation P1=(Q/Cv)2*SG+P2. However when i try to model the second part i end up with a whole bunch of nothing until the P1 hits 5000 and then the Cv of the second part goes which has gone from 10 to 2 in a gradual form goes to .28 in like 1 step (At this point on manual section i'm incrementing Cv by 0.001 per step, so 0.301, 0.300, 0.299.... etc. I'm using a k of 5000 at 1" for the spring. Please see attached spread sheet for rough idea of where i'm at.
For the second Cv i tried to interpolate it from the range deltaP1-2 0-5000, Cv 10-.28 with .28 being the point at which the spring would be fully compressed and maximum desired drop achieved. I'm trying to model this with some degree of accuracy so i don't have to spend thousands and thousands experimenting with different spring strengths and chamber diameters.
Excel File
Image
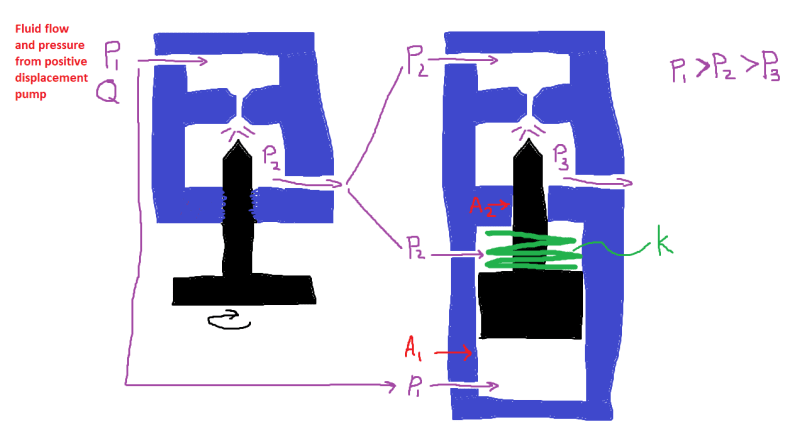