I am looking at an existing two-story residence in a low seismic area where the owner has previously added a CMU enclosed addition with a wood / window end wall (see pictures). But now wants to remove the end wall and place a full height curtain wall in its stead.
My concerns are
A) Lateral stability of the CMU wall ends
B) Getting the roof diagram shear forces down to grade
C) Deflection of the CMU wall ends and tolerances of the curtain wall for such deflection
D) Don’t want to rely on the curtain wall for lateral stability or load transference though it will have some capacity
Unknowns are
A) Is CMU reinforced (to be confirmed via scanning)
B) Joist to CMU connection at roof (to be confirmed via openings)
C) Layout of interior and end shear wall (to be confirmed via site visit)
D) Everything else
Access to
A) Permitted Drawings (unfortunately…almost no structural details…have no idea how it passed review). Doesn't even say if CMU is reinforced or not.
Options
Portal Frame: I could create a portal frame out of steel members to enclose the curtain wall. I’d connect top flange of the portal directly to the deck sheathing. Probably welded moment connection between posts / beam. Carry posts to some footing structure below grade. And bolt the flanges to the existing CMU vertical walls.
Stabilizing Beam: If the existing design, which really does not have a lot of stiffness to it (I don’t really buy that the window framing may act as a deep beam and hence provide a great deal of stiffness…though maybe it is, I don't have an attuned feel for wood construction), we should be able to get away with just restoring the lateral stability to top of the CMU wall. This can be accomplished by a simple spanning beam from CMU wall to CMU wall that I would weld to embedding plates. Basically, the portal frame idea sans posts.
Other Options: Provided by you!!
Notes
If I can get away with just a beam at the top, I’d love it because it’s way cheaper / easier and I won’t have to deal with that CMU wall as it looks like it’s 3” out of plumb (which will be an issue for my portal).
If I go with a portal, I’d have a stiffness mismatch between the portal and the wood shear walls on the other side of the building. Once I verify their construction, I’ll attempt an iterative rigidity analysis to equilibrate the deflections (as much as I can).
Loads are mostly just wind and are quite low so maybe it is all moot and anything will work.
Thoughts?
My concerns are
A) Lateral stability of the CMU wall ends
B) Getting the roof diagram shear forces down to grade
C) Deflection of the CMU wall ends and tolerances of the curtain wall for such deflection
D) Don’t want to rely on the curtain wall for lateral stability or load transference though it will have some capacity
Unknowns are
A) Is CMU reinforced (to be confirmed via scanning)
B) Joist to CMU connection at roof (to be confirmed via openings)
C) Layout of interior and end shear wall (to be confirmed via site visit)
D) Everything else
Access to
A) Permitted Drawings (unfortunately…almost no structural details…have no idea how it passed review). Doesn't even say if CMU is reinforced or not.
Options
Portal Frame: I could create a portal frame out of steel members to enclose the curtain wall. I’d connect top flange of the portal directly to the deck sheathing. Probably welded moment connection between posts / beam. Carry posts to some footing structure below grade. And bolt the flanges to the existing CMU vertical walls.
Stabilizing Beam: If the existing design, which really does not have a lot of stiffness to it (I don’t really buy that the window framing may act as a deep beam and hence provide a great deal of stiffness…though maybe it is, I don't have an attuned feel for wood construction), we should be able to get away with just restoring the lateral stability to top of the CMU wall. This can be accomplished by a simple spanning beam from CMU wall to CMU wall that I would weld to embedding plates. Basically, the portal frame idea sans posts.
Other Options: Provided by you!!
Notes
If I can get away with just a beam at the top, I’d love it because it’s way cheaper / easier and I won’t have to deal with that CMU wall as it looks like it’s 3” out of plumb (which will be an issue for my portal).
If I go with a portal, I’d have a stiffness mismatch between the portal and the wood shear walls on the other side of the building. Once I verify their construction, I’ll attempt an iterative rigidity analysis to equilibrate the deflections (as much as I can).
Loads are mostly just wind and are quite low so maybe it is all moot and anything will work.
Thoughts?
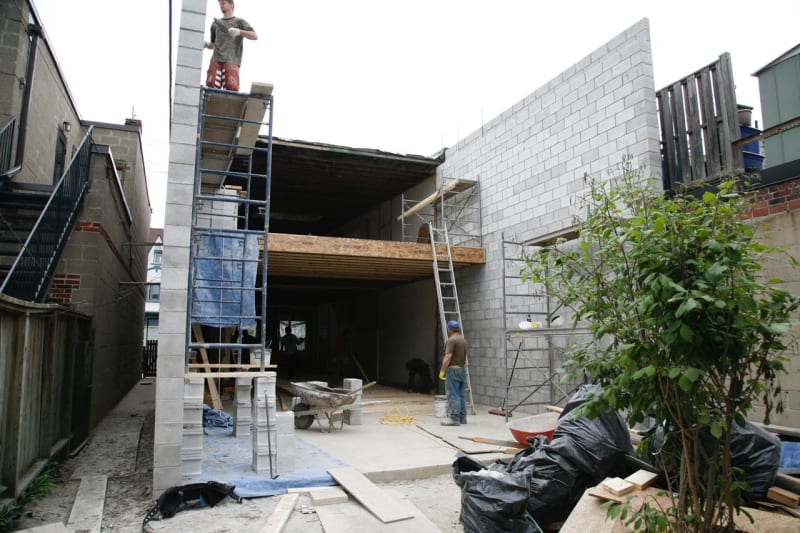
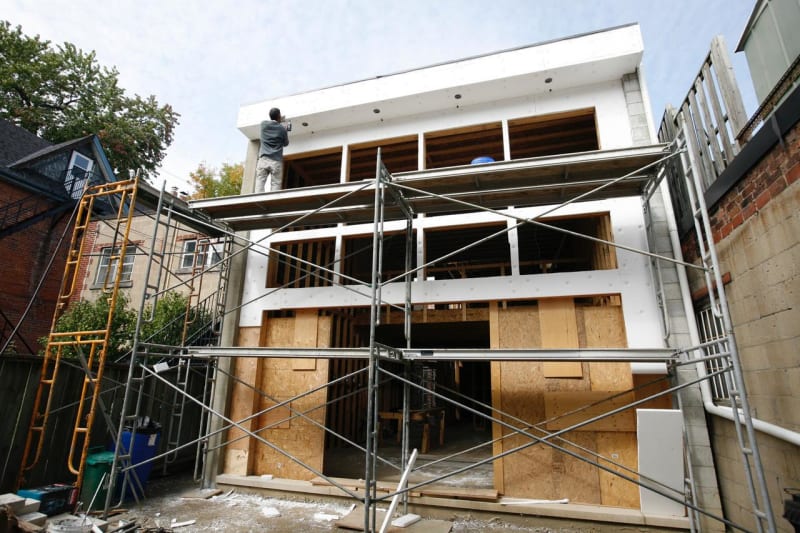