quizzical1
Mechanical
Water changes from ~60F to 150 F every 5 minutes. After a month of cycling between hot and cold, the rig was disassembled and this growth was found. Manifold is Aluminum (2024, not anodized) and the device is 303 SS. Manifold images show before and after cleaning - a wire brush and CLR Mold/Mildew foam was applied multiple times, but its been difficult to remove.
can someone identify the growth, and share insights for cause and prevention?
the discoloration on the cup (brass like appearance, is easily removed when polished) may be evidence of corrosion in addition to the mold issue.
thank you,
can someone identify the growth, and share insights for cause and prevention?
the discoloration on the cup (brass like appearance, is easily removed when polished) may be evidence of corrosion in addition to the mold issue.
thank you,
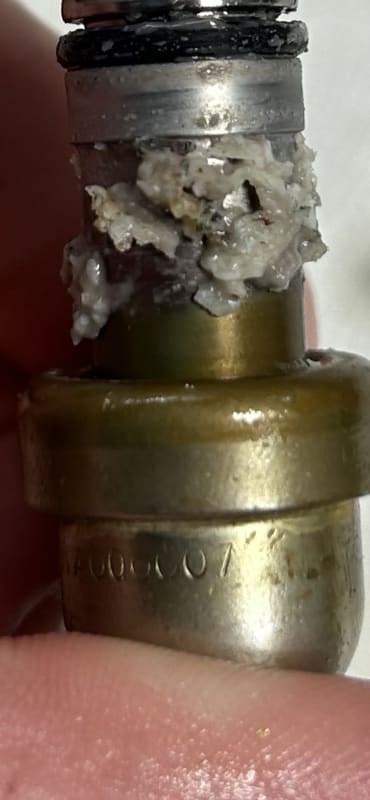
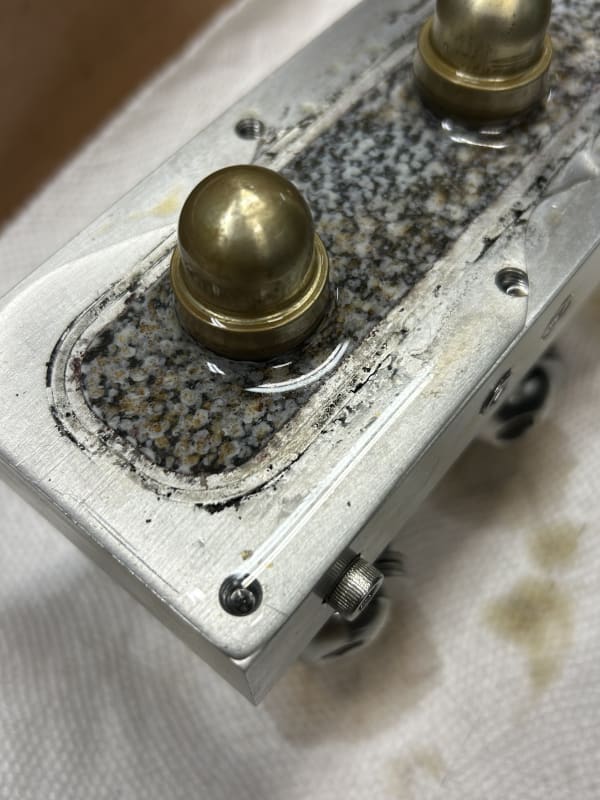
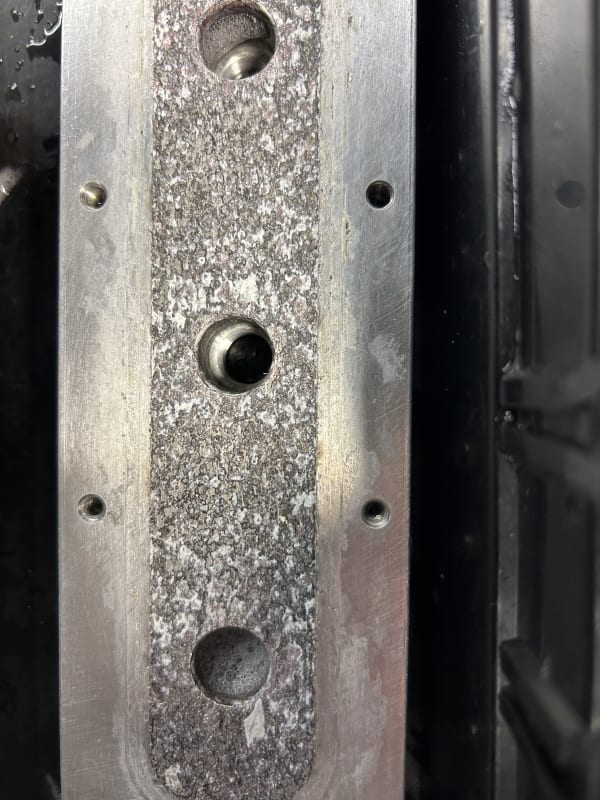