TiCl4
Chemical
- May 1, 2019
- 631
I have a situation that is a bit unusual. I have a need to weld two 3" nozzles onto a 24" B16.5 blind flange. The sketch is below; the design intent is to provide an enlarged portion of piping that would allow liquid monomer droplets that condense in the incoming stream drop out into the bottom portion of piping. Both nozzles are at the top to avoid horizontal runs, which would tend to collect droplets, which would polymerize and plug the pipe. The amount of liquid is minimal (drops per hour), but present a long-term plug hazard that must be dealt with.
Nothing in B16.5 that I've read details multiple nozzle locations on a blind. As such, I think this would be a non-standard part that needs detailed calculation. Not being a mechanical guy myself, I've come for help and guidance.
ASME B31.3, which would be used for this construction, does detail a procedure to check if branch connection reinforcement is needed. I am wondering if there is a similar calculation to be made for the blind to check the pressure/temperature rating. Again, this is a 24" blind (assuming class 150 right now) with a pressure rating (hopefully) of 150 psig.
Can anyone point me in the right direction to applicable codes or calculations for this?
Nothing in B16.5 that I've read details multiple nozzle locations on a blind. As such, I think this would be a non-standard part that needs detailed calculation. Not being a mechanical guy myself, I've come for help and guidance.
ASME B31.3, which would be used for this construction, does detail a procedure to check if branch connection reinforcement is needed. I am wondering if there is a similar calculation to be made for the blind to check the pressure/temperature rating. Again, this is a 24" blind (assuming class 150 right now) with a pressure rating (hopefully) of 150 psig.
Can anyone point me in the right direction to applicable codes or calculations for this?
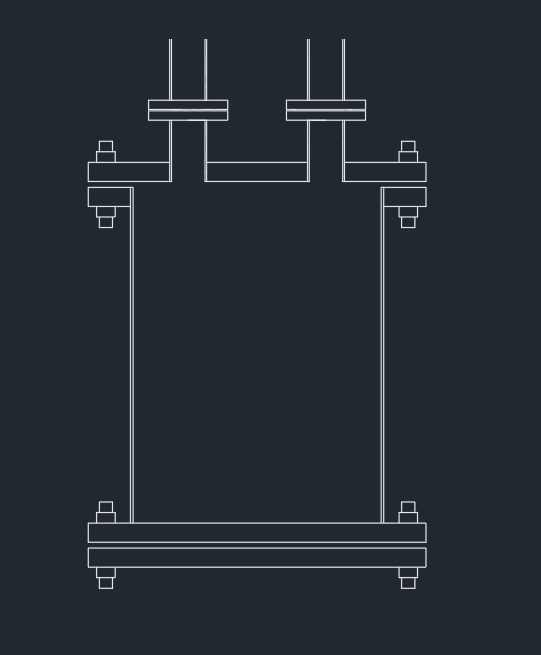