My assumptions:
a) axis of rotation is approx. around the lowest row of anchors
b) only the upper two rows of anchors (total 4) are in tension, the rest are not considered when calculating tension
c) shear force V is equally destributed among anchors
My questions:
1) how do you determine a participating width (b1 in picture) of tension diagonal (in additional vertical steel plate)?
2) how do you control a web of steel beam in tension - again what participating width do you take (b2 in picture)?
3) I calculated tension force in diagonal from force in upper row of anchors as shown bellow - is this OK?
4) I dont know exactly how should I control bottom flange in comppresion?
Id appreciate some comments on my assumptions and answers on my questions.
Tnx in advance.
Bye.
a) axis of rotation is approx. around the lowest row of anchors
b) only the upper two rows of anchors (total 4) are in tension, the rest are not considered when calculating tension
c) shear force V is equally destributed among anchors
My questions:
1) how do you determine a participating width (b1 in picture) of tension diagonal (in additional vertical steel plate)?
2) how do you control a web of steel beam in tension - again what participating width do you take (b2 in picture)?
3) I calculated tension force in diagonal from force in upper row of anchors as shown bellow - is this OK?
4) I dont know exactly how should I control bottom flange in comppresion?
Id appreciate some comments on my assumptions and answers on my questions.
Tnx in advance.
Bye.
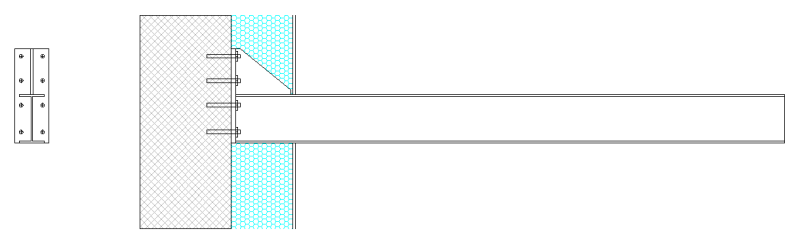
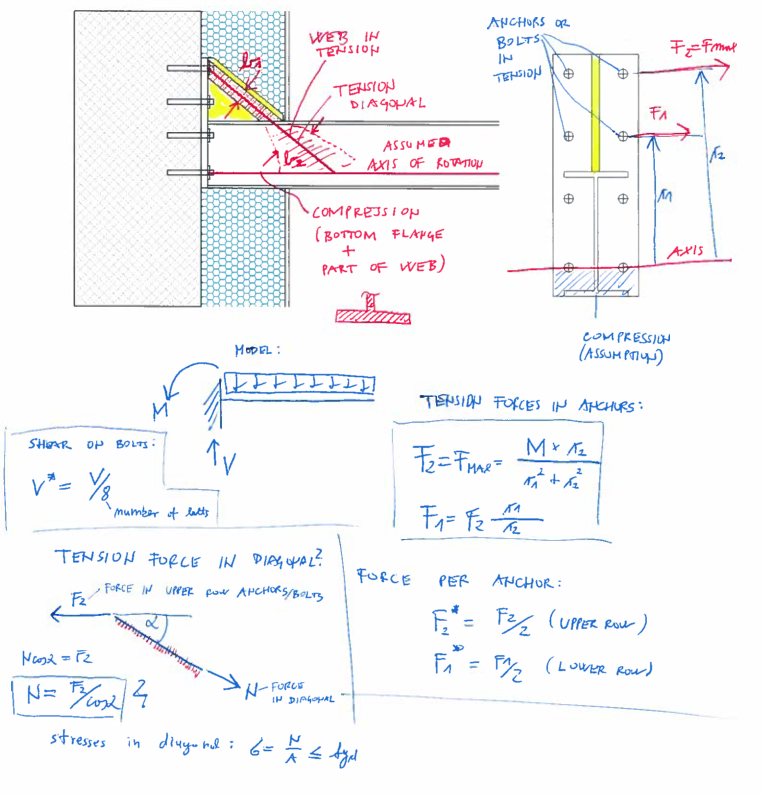