Trying to model a pressure bulkhead like this one
Basically, need some tips on modelling web stiffeners with minimal effort & time. I want to make the stiffener spacing parametric so if I need to make any changes in spacing, it would be easier. I am thinking of drawing all the stiffener lines in one sketch with dimensional constraints and use output feature for each lines and use ribs or pad features with thickness for solid modelling. Is there any better way of accomplishing the above?
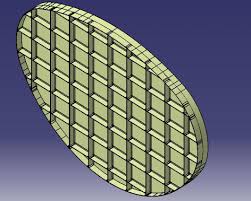
Basically, need some tips on modelling web stiffeners with minimal effort & time. I want to make the stiffener spacing parametric so if I need to make any changes in spacing, it would be easier. I am thinking of drawing all the stiffener lines in one sketch with dimensional constraints and use output feature for each lines and use ribs or pad features with thickness for solid modelling. Is there any better way of accomplishing the above?