PaulKraemer
Electrical
- Jan 13, 2012
- 145
Hi,
I am working on the electrical design for a small machine that will have a single VFD that drives an AC motor. The VFD has an integrated EMC filter and is CE approved. I have hired CE consultants to oversee my design process and (hopefully) give us the go ahead to put a CE mark on our machine after it is built. For my motor power cable, I will be using a VFD rated shielded cable with four conductors (three current carrying conductors plus a green/yellow ground conductor). This cable would go from the VFD to terminal blocks in my electrical enclosure, and then from these terminal blocks out of the electrical enclosure to the motor. I like to include terminal blocks for my motor cables because it allows my panel builder to neatly run the cable from the drive to the terminal blocks, simplifying the connections that I have to make after the enclosure is installed. It also simplifies maintenance should my customer ever want to disconnect cables from the enclosure for some reason. My originally planned motor power circuit is as shown on the following illustration:
As can be seen on the illustration, my original plan was to land both the green/yellow ground wire and the shield at all three of the following locations:
[ol 1]
[li]At the ground terminal of the VFD (DRV1)[/li]
[li]At the ground terminal block[/li]
[li]At the ground screw in the motor’s built-in conduit box[/li]
[/ol]
When I presented this plan to the CE consultants, they told me that EMI or shield grounds should be isolated from the main safety ground. The purpose they say for this separation is that all of the noise being filtered out of the AC line by my filter is shuttled to the main safety ground plane. If I tie my shield ground to the same point electrically, that noise will likely travel on the drain wire out the the device. They say one way they have seen this addressed is with a ground bus bar mounted on isolating (thermoplastic) hardware. There is enough dead metal to dissipate the noise but is reliably separated from the main ground.
He says the termination point would be as follows:
I am just wondering if anyone here knows of any manufacturers that might sell hardware specifically designed for this type of noiseless / clean ground of cable shields?
Any suggestions will be greatly appreciated.
Thanks in advance,
Paul
I am working on the electrical design for a small machine that will have a single VFD that drives an AC motor. The VFD has an integrated EMC filter and is CE approved. I have hired CE consultants to oversee my design process and (hopefully) give us the go ahead to put a CE mark on our machine after it is built. For my motor power cable, I will be using a VFD rated shielded cable with four conductors (three current carrying conductors plus a green/yellow ground conductor). This cable would go from the VFD to terminal blocks in my electrical enclosure, and then from these terminal blocks out of the electrical enclosure to the motor. I like to include terminal blocks for my motor cables because it allows my panel builder to neatly run the cable from the drive to the terminal blocks, simplifying the connections that I have to make after the enclosure is installed. It also simplifies maintenance should my customer ever want to disconnect cables from the enclosure for some reason. My originally planned motor power circuit is as shown on the following illustration:
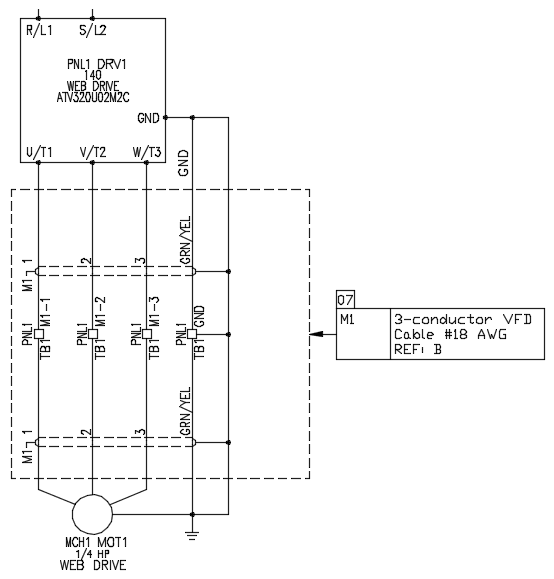
As can be seen on the illustration, my original plan was to land both the green/yellow ground wire and the shield at all three of the following locations:
[ol 1]
[li]At the ground terminal of the VFD (DRV1)[/li]
[li]At the ground terminal block[/li]
[li]At the ground screw in the motor’s built-in conduit box[/li]
[/ol]
When I presented this plan to the CE consultants, they told me that EMI or shield grounds should be isolated from the main safety ground. The purpose they say for this separation is that all of the noise being filtered out of the AC line by my filter is shuttled to the main safety ground plane. If I tie my shield ground to the same point electrically, that noise will likely travel on the drain wire out the the device. They say one way they have seen this addressed is with a ground bus bar mounted on isolating (thermoplastic) hardware. There is enough dead metal to dissipate the noise but is reliably separated from the main ground.
He says the termination point would be as follows:

I am just wondering if anyone here knows of any manufacturers that might sell hardware specifically designed for this type of noiseless / clean ground of cable shields?
Any suggestions will be greatly appreciated.
Thanks in advance,
Paul