Currently in the midst of an investigation into the failure of a high pressure booster pump. Today I was finally able to eyes on broken impellers. The pump is scheduled to deliver filtered sea water into RO membranes pressure vessels.
Pump details:
Energy Recovery Inc.
Model: HP-2403
3 stage centrifugal
300 GPM @50 psi
Boosting from 700 psi to 750 psi.
20 HP
We have had multiple failures in 4 pumps. Failures are occuring 2-3 weeks after startup.
Markings on the destroyed impellers along with testimony that VFDs are ramping up speed or hunting within hours of failure lead me to believe failure is due to contact between the impellers and housing. Tomorrow we are going to investigate further why this contact is occuring.
Now to the thread title and reason for this thread; per pump specification and submittal data the impellers are made of Noryl. Googling Noryl, I find evidence that this material can "absorb" water. Is this right? When used for a pump's impeller, does material expansion need to be considered as a possibility in these failures?
I've also notice white discoloration. I'm not completely convinced the discoloration is due to rubbing or a result of chemical interaction. What, if any chemicals can have an impact on the properties of Noryl plastic? Or just cause some discoloration?
Gonna keep searching Google results, there is just so much information out there finding what I am looking for is like finding a needle in a hay stack. If someone here can help me narrow my search, I would appreciate it.
Attached photos are of multiple failed impellers, when more than one piece is in a photo, there is no guarntee or promise that the pieces are from the same impeller.
Pump details:
Energy Recovery Inc.
Model: HP-2403
3 stage centrifugal
300 GPM @50 psi
Boosting from 700 psi to 750 psi.
20 HP
We have had multiple failures in 4 pumps. Failures are occuring 2-3 weeks after startup.
Markings on the destroyed impellers along with testimony that VFDs are ramping up speed or hunting within hours of failure lead me to believe failure is due to contact between the impellers and housing. Tomorrow we are going to investigate further why this contact is occuring.
Now to the thread title and reason for this thread; per pump specification and submittal data the impellers are made of Noryl. Googling Noryl, I find evidence that this material can "absorb" water. Is this right? When used for a pump's impeller, does material expansion need to be considered as a possibility in these failures?
I've also notice white discoloration. I'm not completely convinced the discoloration is due to rubbing or a result of chemical interaction. What, if any chemicals can have an impact on the properties of Noryl plastic? Or just cause some discoloration?
Gonna keep searching Google results, there is just so much information out there finding what I am looking for is like finding a needle in a hay stack. If someone here can help me narrow my search, I would appreciate it.
Attached photos are of multiple failed impellers, when more than one piece is in a photo, there is no guarntee or promise that the pieces are from the same impeller.
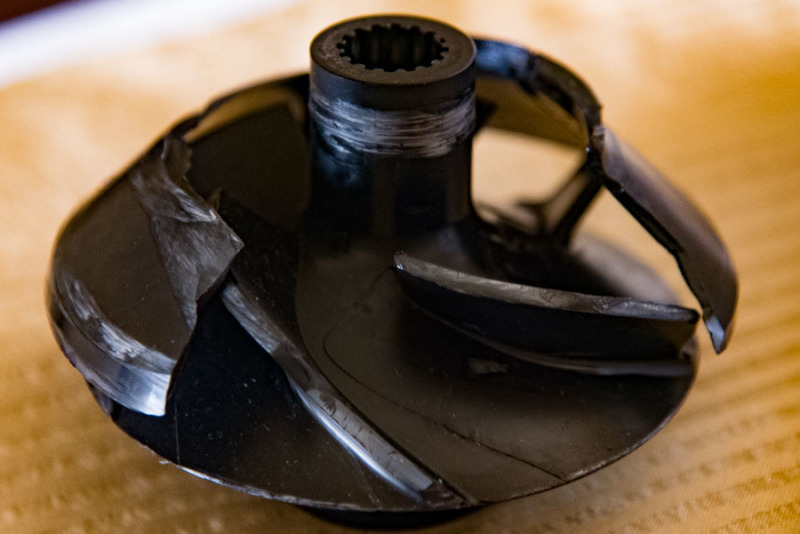
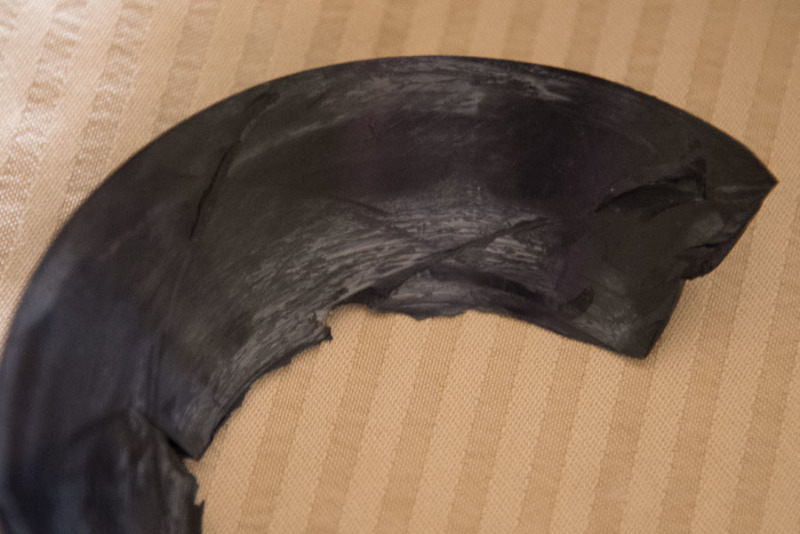
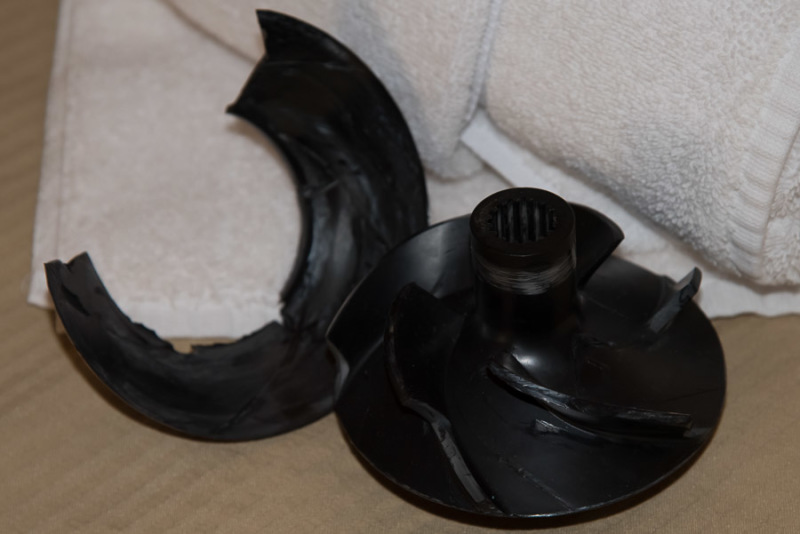
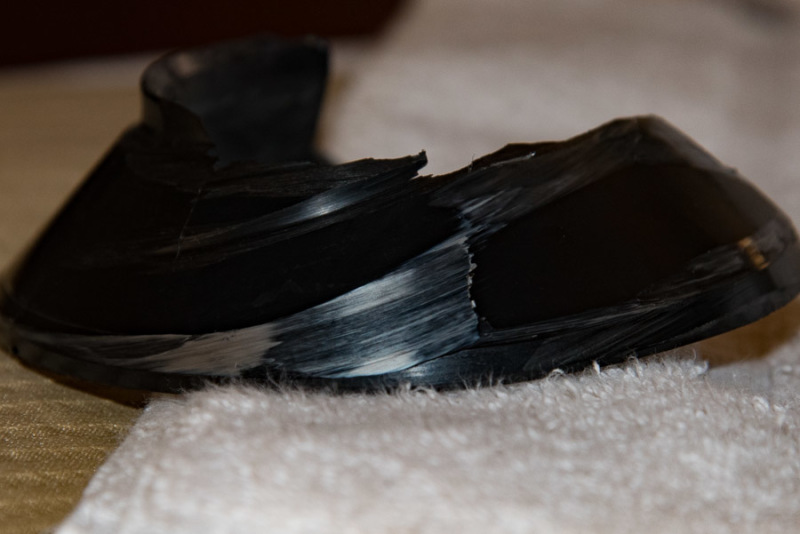
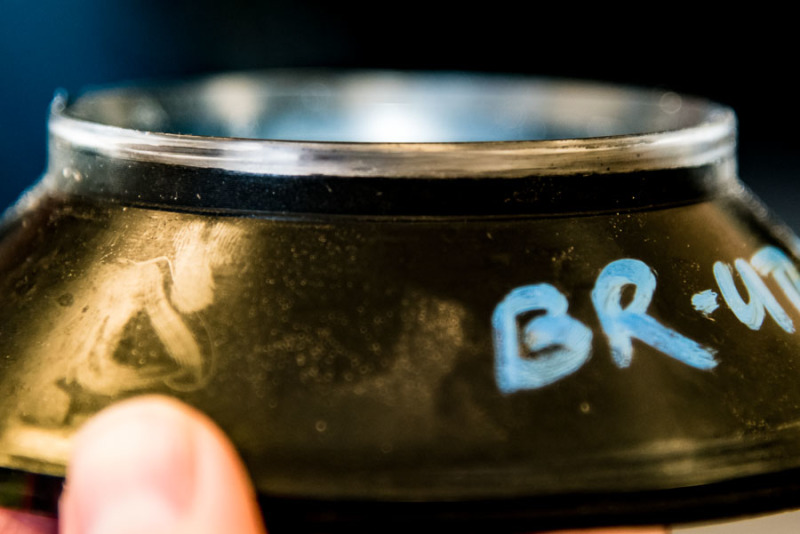