g.alshamsi
Civil/Environmental
Hello all, so here's my issue: I have a cold-formed steel shear wall made up of a frame and a thin sheathing (0.8 mm) subjected to a quasi-static cyclic loading protocol. Let's call this experiment one.
After the experiment is complete, the sheathing was manually cutout from the frame as shown in the following figures; Then the frame was subjected to another cyclic loading protocol (let's call this experiment 2).
I was able to simulate experiment one with acceptable results using s4r elements, linear kinematic hardening and the explicit solver. My issue is on how to proceed from here to simulate experiment 2. The main challenge is to model the inelastic deformations/strains that were generated from the cyclic loading from experiment 1. I'm thinking of building a model where the sheathing is cutout from the centre of the frame and subjecting it to two quasi-static displacement load protocols using two separate steps. I'm uncertain however if this method would give acceptable results or even work the way I want it to. If anyone has any recommendations or have previous experience with something similar, feel free to add your own thought/recommendations.
Thanks for your time, cheers!
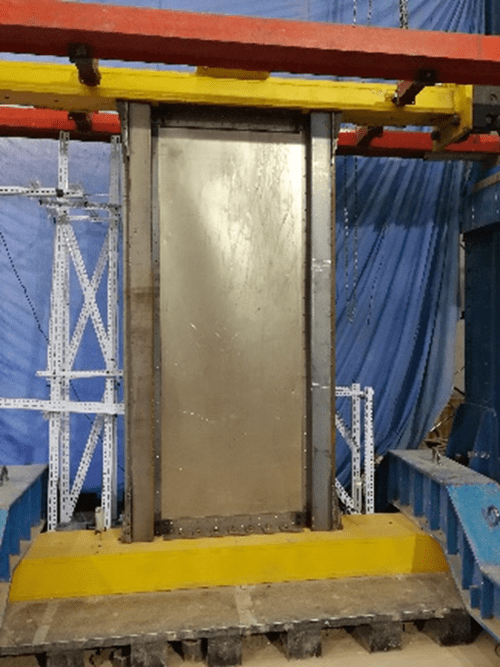
After the experiment is complete, the sheathing was manually cutout from the frame as shown in the following figures; Then the frame was subjected to another cyclic loading protocol (let's call this experiment 2).
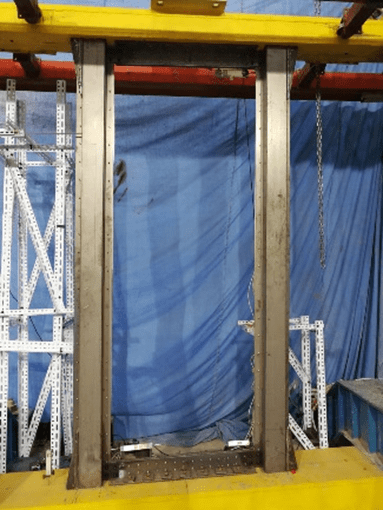
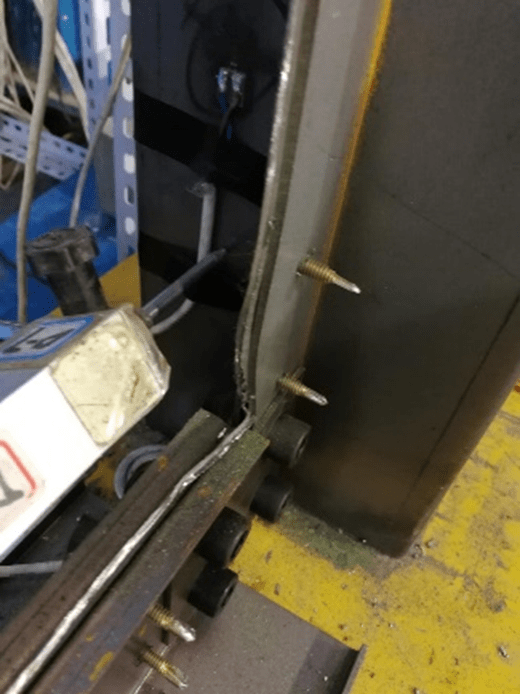
I was able to simulate experiment one with acceptable results using s4r elements, linear kinematic hardening and the explicit solver. My issue is on how to proceed from here to simulate experiment 2. The main challenge is to model the inelastic deformations/strains that were generated from the cyclic loading from experiment 1. I'm thinking of building a model where the sheathing is cutout from the centre of the frame and subjecting it to two quasi-static displacement load protocols using two separate steps. I'm uncertain however if this method would give acceptable results or even work the way I want it to. If anyone has any recommendations or have previous experience with something similar, feel free to add your own thought/recommendations.
Thanks for your time, cheers!