IdanPV
Mechanical
- Aug 26, 2019
- 473
Hello all,
I have a question regarding a nozzle to shell welding in an ASME "U" vessel.
The weld detail is similar to that shown in ASME VIII-2 Table 4.2.12 detail 3/ASME VIII-1 Figure UW-16.1(z-1) except that there is no bevel in the shell, and the shell is completely straight.
See illustration below (ignore the "tc" marking please)
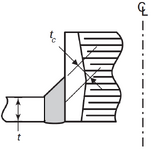
1. Is this kind of weld detail is acceptable?
2. What would be the correct symbol for this weld as per AWS and ISO.
Thanks,
I have a question regarding a nozzle to shell welding in an ASME "U" vessel.
The weld detail is similar to that shown in ASME VIII-2 Table 4.2.12 detail 3/ASME VIII-1 Figure UW-16.1(z-1) except that there is no bevel in the shell, and the shell is completely straight.
See illustration below (ignore the "tc" marking please)
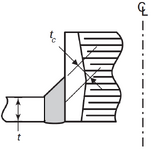
1. Is this kind of weld detail is acceptable?
2. What would be the correct symbol for this weld as per AWS and ISO.
Thanks,
Last edited: