So I'm designing a co-gen power system for an off grid remote research building. I'm not really sure where to begin- I need a few pointers/guidance on where to start...
Does this look like a good design? Should I get creative with how the gensets are interconnected?
Or just keep things really basic?
Anything I've missed? Go/no go? Or am I way off?
Power is normally produced by natural gas and solar with onsite diesel tanks to meet the requirements of article 700.
Does this look like a good design? Should I get creative with how the gensets are interconnected?
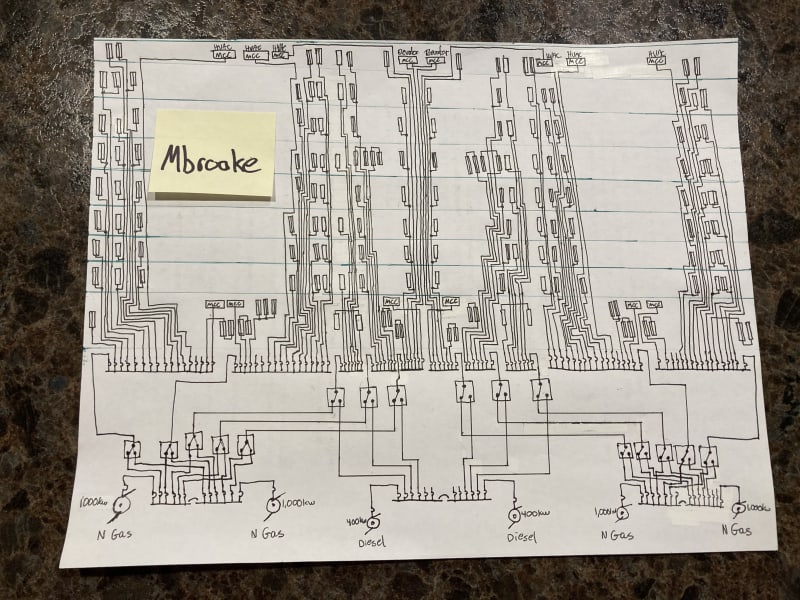
Or just keep things really basic?
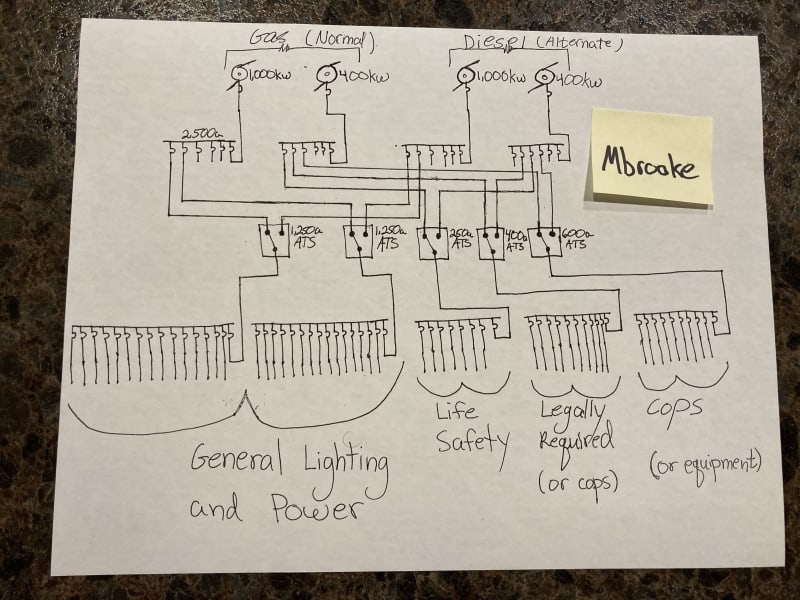
Anything I've missed? Go/no go? Or am I way off?
Power is normally produced by natural gas and solar with onsite diesel tanks to meet the requirements of article 700.