-
1
- #1
Dear All, respected valve professionals,
This post may seem contradictive with my previous postings, but I believe that there is some time in our career when we were outnumbered by our non-valve peers and requires “relatively equal” sparing partners to check whether we are still insane.
I am working in a country where “10 How’s” and “10 Why’s/Why not” always asked to challenge one’s experiences. In addition, we are now living in an era where instant solutions is seemingly possible and it is a big word to say NO based on gut feeling.
Never had any experience with solving problem one below in live situation, and never meet people who dare or even survive to tell the story, kindly advise what is the wise (if not the best) way to convey the message.
PS: I've seen this problem several times per year, ever since I started to repair valve (15 years ago), up until now it was up to my team on how to tackle it. But nowadays trend is: "can we do it without killing the Plant??"
1.Problem number one with damage spindle.
Root cause: operator was using some “tool” sort of electro pneumatic “gun” and forgot to stop in close position
Valve general: 4”-2500# gate valve, material SS321, welded, Schedule XXS
Try to see underneath to check whether the bottom spindle crooked or not, the slot between stem and wedge still intact and whether the gland packing rings is borne unequal axial force. No luck, due to wall thickness is 69 mm up to 100 mm we can only see grey area even with the strongest Gamma ray
What is inside: Gas with 5% H2S and some other nasty stuff, pressure 180 bar
Crazy idea which I am outnumbered is my colleagues are figuring out on how to straightening it as current condition without shutting down the Plant. By means of making specific threaded hydraulic jack (which on the making). We will test it on the mockup first, bend one representable valve in the workshop and put it on the test bench, under pressure, and straightening it.
Question:
Is it even possible to do this?
What could go wrong with the mock up and real test? Gland packing wise, and what the simple explanation behind it?
Any “wise” words?
2.Problem number two with cracked open gearbox
Quite straight forward: nodular cast iron gearbox housing, even though valve is manually operated (in theory do not see shock compared to its actuated brother) but after more than 25 years things like this just happened
Constraint: RingO pressure seal (no longer exist) and lead time (3 weeks)
Question: what is better material solutions? Quantity is only 40 something actuator, is another brand usually interchangeable?
Open for mocking, laughter, etc. but preferably constructive advice.![[peace] [peace] [peace]](/data/assets/smilies/peace.gif)
Thank you,
Regards,
MR
All valves will last for years, except the ones that were poorly manufactured; are still wrongly operated and or were wrongly selected
This post may seem contradictive with my previous postings, but I believe that there is some time in our career when we were outnumbered by our non-valve peers and requires “relatively equal” sparing partners to check whether we are still insane.
I am working in a country where “10 How’s” and “10 Why’s/Why not” always asked to challenge one’s experiences. In addition, we are now living in an era where instant solutions is seemingly possible and it is a big word to say NO based on gut feeling.
Never had any experience with solving problem one below in live situation, and never meet people who dare or even survive to tell the story, kindly advise what is the wise (if not the best) way to convey the message.
PS: I've seen this problem several times per year, ever since I started to repair valve (15 years ago), up until now it was up to my team on how to tackle it. But nowadays trend is: "can we do it without killing the Plant??"
1.Problem number one with damage spindle.
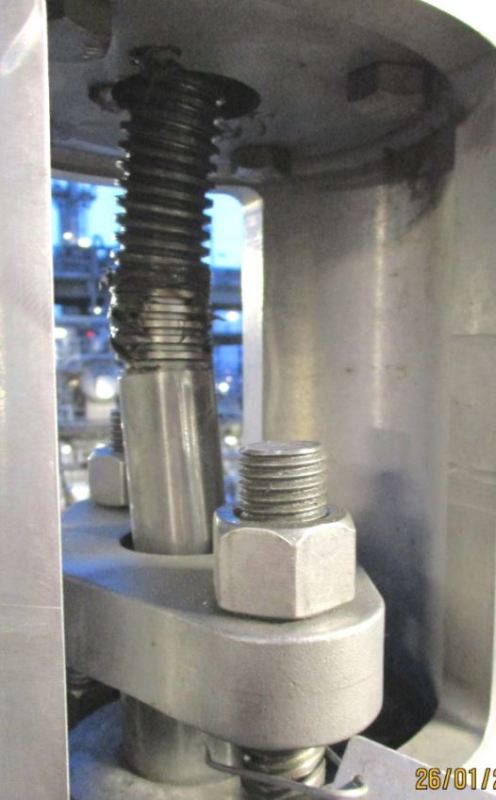
Root cause: operator was using some “tool” sort of electro pneumatic “gun” and forgot to stop in close position
Valve general: 4”-2500# gate valve, material SS321, welded, Schedule XXS
Try to see underneath to check whether the bottom spindle crooked or not, the slot between stem and wedge still intact and whether the gland packing rings is borne unequal axial force. No luck, due to wall thickness is 69 mm up to 100 mm we can only see grey area even with the strongest Gamma ray
What is inside: Gas with 5% H2S and some other nasty stuff, pressure 180 bar
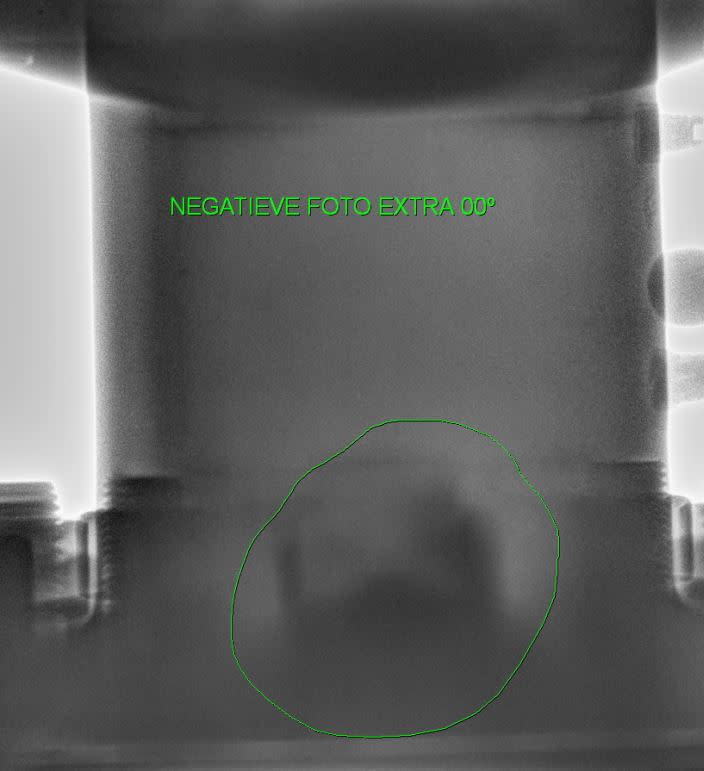
Crazy idea which I am outnumbered is my colleagues are figuring out on how to straightening it as current condition without shutting down the Plant. By means of making specific threaded hydraulic jack (which on the making). We will test it on the mockup first, bend one representable valve in the workshop and put it on the test bench, under pressure, and straightening it.
Question:
Is it even possible to do this?
What could go wrong with the mock up and real test? Gland packing wise, and what the simple explanation behind it?
Any “wise” words?
2.Problem number two with cracked open gearbox
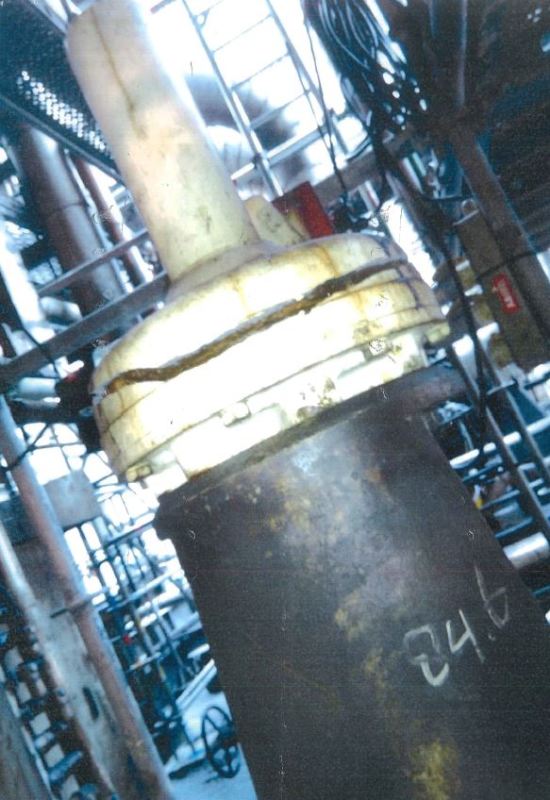
Quite straight forward: nodular cast iron gearbox housing, even though valve is manually operated (in theory do not see shock compared to its actuated brother) but after more than 25 years things like this just happened
Constraint: RingO pressure seal (no longer exist) and lead time (3 weeks)
Question: what is better material solutions? Quantity is only 40 something actuator, is another brand usually interchangeable?
Open for mocking, laughter, etc. but preferably constructive advice.
![[peace] [peace] [peace]](/data/assets/smilies/peace.gif)
Thank you,
Regards,
MR
All valves will last for years, except the ones that were poorly manufactured; are still wrongly operated and or were wrongly selected