JAE
Structural
- Jun 27, 2000
- 15,577
We recently came across an question in steel weld design and forwarded this to AISC for their response.
I thought I'd post it here to see what others think:
[blue]We are trying to design a beam-to-column connection using a seat under the beam. The concept is to also include a top flange clip angle to laterally stabilize the beam and also to help the beam take some significant out-of-plane lateral load into the column.
However, there appears to be an inconsistency in the AISC Steel Manual and Specification (360-16 – 15th Edition Manual). In the commentary of Section J2.2b, there is a discussion about single sided fillet welds in joints subject to rotation about the toe of the weld, or the weld axis. The commentary illustrates this with Figure C-J2.3(b). Also, in the manual, on page 8-17, there is also discussion of one-sided fillet welds, referencing Figure 8-10, and showing the concern for the crack initiation at the root of the weld due to the plate-to-plate interface creating a stress raiser point.
However, in Part 10 of the same manual, on page 10-69, for Unstiffened Seated Connections, Figure 10-7(b) clearly illustrates a top flange brace angle with welds only at the toe of each angle leg, one to the column and one to the beam. The beams in this illustration will rotate under load, pulling the angle such that the toe of the weld at the top of the angle will rotate as warned against by the previously quoted sections.
We have also seen other AISC resources, details, etc. that also suggest that the angle toe-welds like this are permissible.
Can you clarify why these may or may not be inconsistent? Is there a particular aspect of the angle welds in Figure 10-7(b) that allow this? Is there perhaps a limit on rotation that a weld can take despite being a single-sided weld?[/blue]
I thought I'd post it here to see what others think:
[blue]We are trying to design a beam-to-column connection using a seat under the beam. The concept is to also include a top flange clip angle to laterally stabilize the beam and also to help the beam take some significant out-of-plane lateral load into the column.
However, there appears to be an inconsistency in the AISC Steel Manual and Specification (360-16 – 15th Edition Manual). In the commentary of Section J2.2b, there is a discussion about single sided fillet welds in joints subject to rotation about the toe of the weld, or the weld axis. The commentary illustrates this with Figure C-J2.3(b). Also, in the manual, on page 8-17, there is also discussion of one-sided fillet welds, referencing Figure 8-10, and showing the concern for the crack initiation at the root of the weld due to the plate-to-plate interface creating a stress raiser point.
However, in Part 10 of the same manual, on page 10-69, for Unstiffened Seated Connections, Figure 10-7(b) clearly illustrates a top flange brace angle with welds only at the toe of each angle leg, one to the column and one to the beam. The beams in this illustration will rotate under load, pulling the angle such that the toe of the weld at the top of the angle will rotate as warned against by the previously quoted sections.
We have also seen other AISC resources, details, etc. that also suggest that the angle toe-welds like this are permissible.
Can you clarify why these may or may not be inconsistent? Is there a particular aspect of the angle welds in Figure 10-7(b) that allow this? Is there perhaps a limit on rotation that a weld can take despite being a single-sided weld?[/blue]
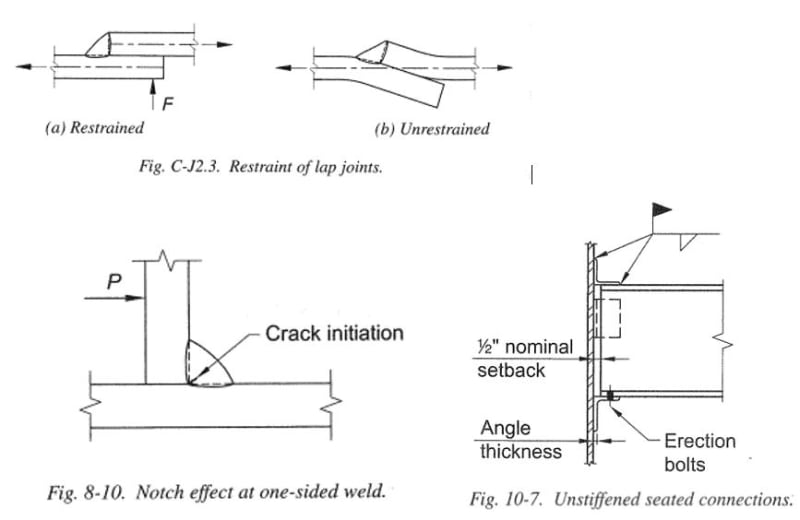