Dianium
Structural
- May 19, 2016
- 3
What precisely are the causes of the concrete discoloration. I have a seawall cap I am working with, and it appears that cracks have developed along the top and sides at approximately 24" to 30" o/c. I have also noted that there is discoloration of the concrete as well as pattern discoloration in some locations.
My initially thoughts are the lack of control joints caused the cracks and perhaps pouring on top of an existing CMU wall where the cause, but after seeing the discoloration, I think it's something else. I have attached pictures to help visualize what is happening.
My initially thoughts are the lack of control joints caused the cracks and perhaps pouring on top of an existing CMU wall where the cause, but after seeing the discoloration, I think it's something else. I have attached pictures to help visualize what is happening.

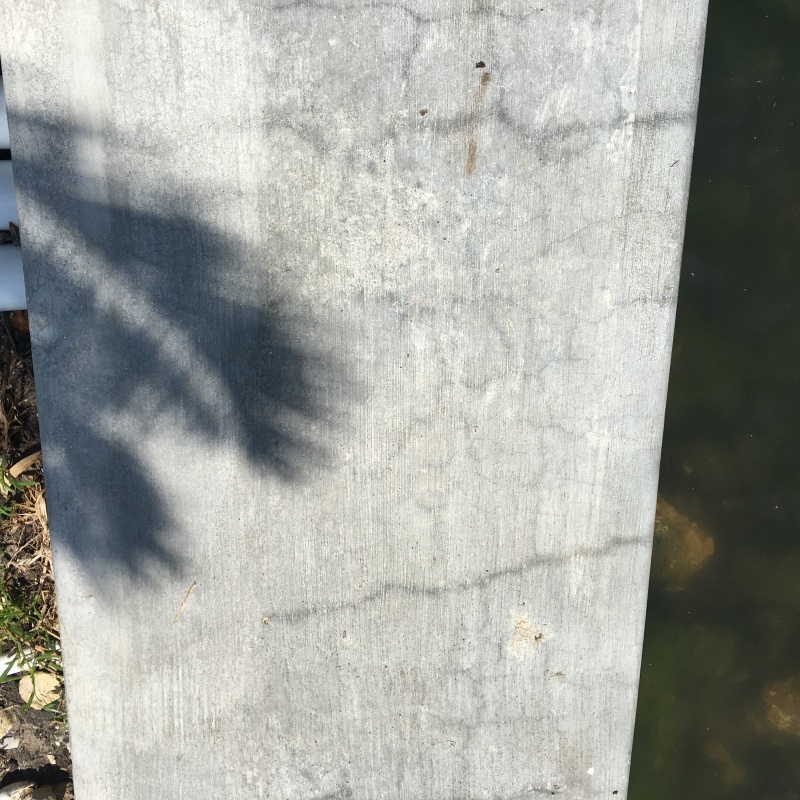
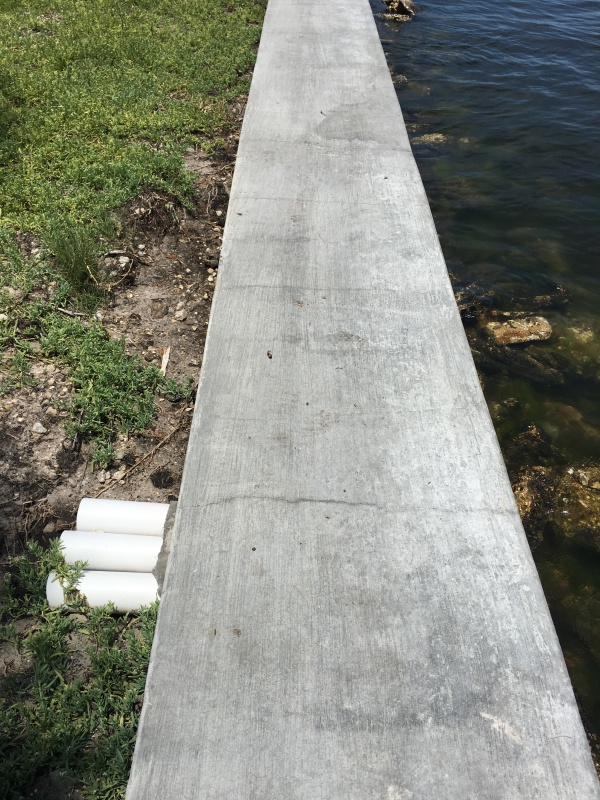