Tuco_Salman
Automotive
Hello All,
I am new to this forum and this is my first question.
I tried searching about this in the forum and please pardon me if it is already asked/posted.
My first question is that what is the significance of the patterns found in auto rickshaw body?
Does the patterns help in giving rigidity to the structure? ( Look at the below images)
What is the purpose of these patterns?
I am trying to build replica of this body design in solidworks using solidworks sheet metal.
My second question is that how to build these patterns in solidworks sheet metal?
Thanks
Tuco
I am new to this forum and this is my first question.
I tried searching about this in the forum and please pardon me if it is already asked/posted.
My first question is that what is the significance of the patterns found in auto rickshaw body?
Does the patterns help in giving rigidity to the structure? ( Look at the below images)
What is the purpose of these patterns?
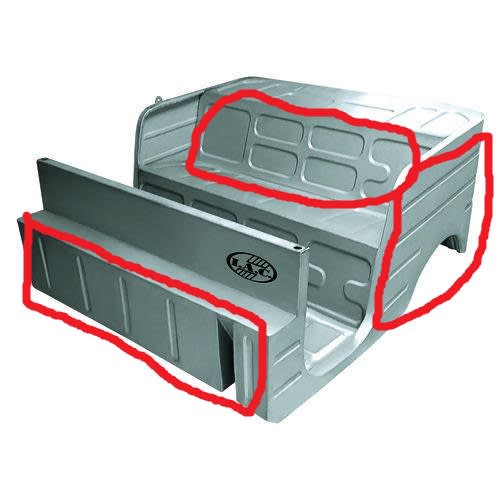
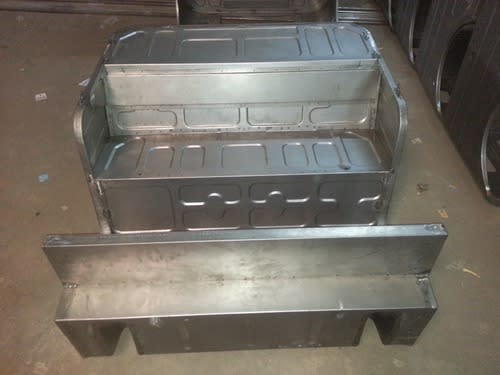
I am trying to build replica of this body design in solidworks using solidworks sheet metal.
My second question is that how to build these patterns in solidworks sheet metal?
Thanks
Tuco