Hi guys,
I've come across a problem which I can't seem to find an answer to online.
Is there any difference between the method of sizing pipe with water flow (say chilled/condenser water) or gas flow or vacuum air flow?
The reason I ask this is because of the following attached charts from a handbook I use.
1. Looking at the water chart, the X-axis has a pressure drop per metre, and based on the flow rate I can select a nominal pipe diameter. I've used this extensively in my CHW/CDW designs and understand how to use it.
2. Looking at the gas and vacuum pipe sizer charges, can someone please explain for the gas chart what the "Distance from source at 1.125kPa for 75Pa pressure loss" means? My understanding of this is that the 1.125kPa is the available pressure in the system from some sort of pump. But what is the 75Pa pressure loss? There is a similar title for the vaccuum chart.
3. Why is the chart for gas and vaccuum different to the water chart? Is a different method used to size gas/vaccuum pipes? Is this using the "longest run method"?
Cheers
I've come across a problem which I can't seem to find an answer to online.
Is there any difference between the method of sizing pipe with water flow (say chilled/condenser water) or gas flow or vacuum air flow?
The reason I ask this is because of the following attached charts from a handbook I use.
1. Looking at the water chart, the X-axis has a pressure drop per metre, and based on the flow rate I can select a nominal pipe diameter. I've used this extensively in my CHW/CDW designs and understand how to use it.
2. Looking at the gas and vacuum pipe sizer charges, can someone please explain for the gas chart what the "Distance from source at 1.125kPa for 75Pa pressure loss" means? My understanding of this is that the 1.125kPa is the available pressure in the system from some sort of pump. But what is the 75Pa pressure loss? There is a similar title for the vaccuum chart.
3. Why is the chart for gas and vaccuum different to the water chart? Is a different method used to size gas/vaccuum pipes? Is this using the "longest run method"?
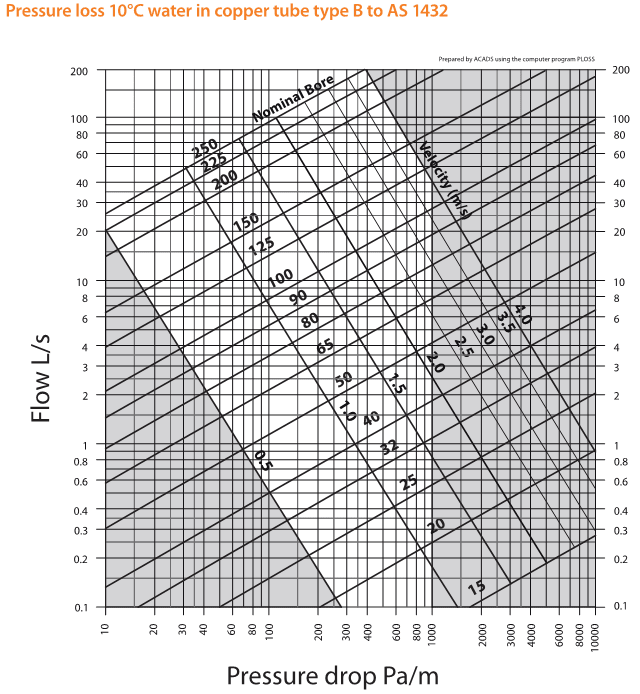
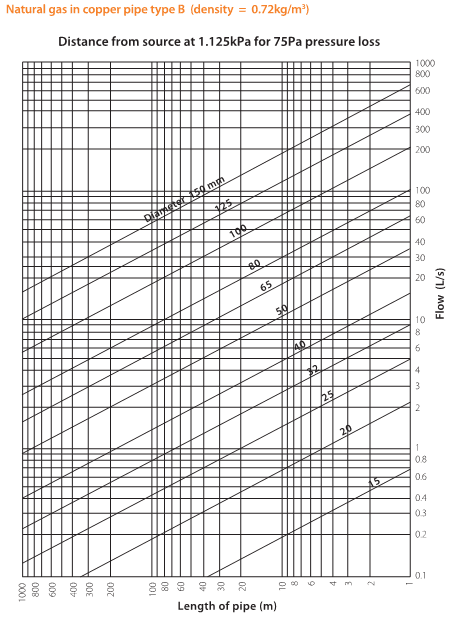
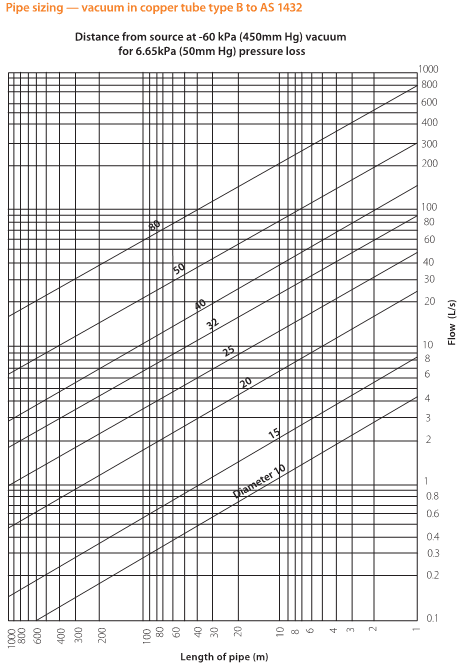
Cheers