Hi,
I've been given a "legacy project" which consists of designing a pressure vessel, meant to hold 1.5 bar absolute pressure of N2 or 0.5 absolute air pressure.
The are 3 design constraints that make this task problematic:
1) The vessel must be made of plastic or glass because of RF issues.
2) The vessel is meant to hold a round PCB, which has a 250 mm diameter. which is an issue because of (3)
3) The vessel will be placed in an oven with an internal dimension of 278 mm. the oven will reach a max of 60 deg C.
This means, in order both to fully encase the PCB and also fit in the oven, the ID has to be 250, with an OD of around 275 mm. which gives it a wall thickness of about 12.5 mm.
my second option is to clamp the pcb between 2 cylinderical , and equalize the pressure between them (see pic). doing this allows my minimal ID to reach 180 mm (WT of up to 35 mm). and the PCB actually has through holes meant for bolts.
after all this, my questions are:
*do you think this is feasible? I'm wary of using plastic for pressure holding applications, especially with heat involved.
*If so, Which material would you use? I was thinking polycarbonate, since it tends to stretch rather than shatter when failing.
*Which WT do you think would be good? I've done the calculations, and obviously 35 mm WT is over designed. But in this case I would like to make this as robust as possible.
In general - I've looked through the PVHO safety standards, which speaks more about acrylic viewing windows. But besides that there are very few references on applications like these. I've also found some OTS options, but they don't fit my constraints as they are today.
Thanks in advance.
I've been given a "legacy project" which consists of designing a pressure vessel, meant to hold 1.5 bar absolute pressure of N2 or 0.5 absolute air pressure.
The are 3 design constraints that make this task problematic:
1) The vessel must be made of plastic or glass because of RF issues.
2) The vessel is meant to hold a round PCB, which has a 250 mm diameter. which is an issue because of (3)
3) The vessel will be placed in an oven with an internal dimension of 278 mm. the oven will reach a max of 60 deg C.
This means, in order both to fully encase the PCB and also fit in the oven, the ID has to be 250, with an OD of around 275 mm. which gives it a wall thickness of about 12.5 mm.
my second option is to clamp the pcb between 2 cylinderical , and equalize the pressure between them (see pic). doing this allows my minimal ID to reach 180 mm (WT of up to 35 mm). and the PCB actually has through holes meant for bolts.
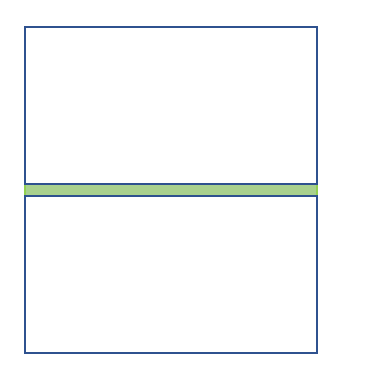
after all this, my questions are:
*do you think this is feasible? I'm wary of using plastic for pressure holding applications, especially with heat involved.
*If so, Which material would you use? I was thinking polycarbonate, since it tends to stretch rather than shatter when failing.
*Which WT do you think would be good? I've done the calculations, and obviously 35 mm WT is over designed. But in this case I would like to make this as robust as possible.
In general - I've looked through the PVHO safety standards, which speaks more about acrylic viewing windows. But besides that there are very few references on applications like these. I've also found some OTS options, but they don't fit my constraints as they are today.
Thanks in advance.