I'm trying to reassemble a 4 section double pole switch I disassembled.
I need to backup and understand the internal wiring of the motor.
I found a diagram of a motor that I think is wired for 240V, and then I made a drawing
of what I think it would look like when changes to 120V operation.
Can anyone confirm I have it right so far?
I need to backup and understand the internal wiring of the motor.
I found a diagram of a motor that I think is wired for 240V, and then I made a drawing
of what I think it would look like when changes to 120V operation.
Can anyone confirm I have it right so far?
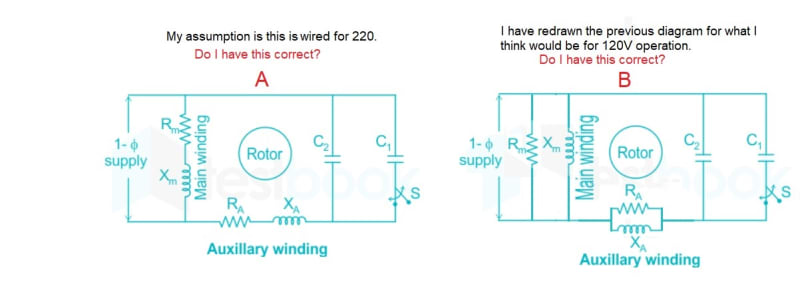